Mercilessly efficient:
Productivity from start to finish.
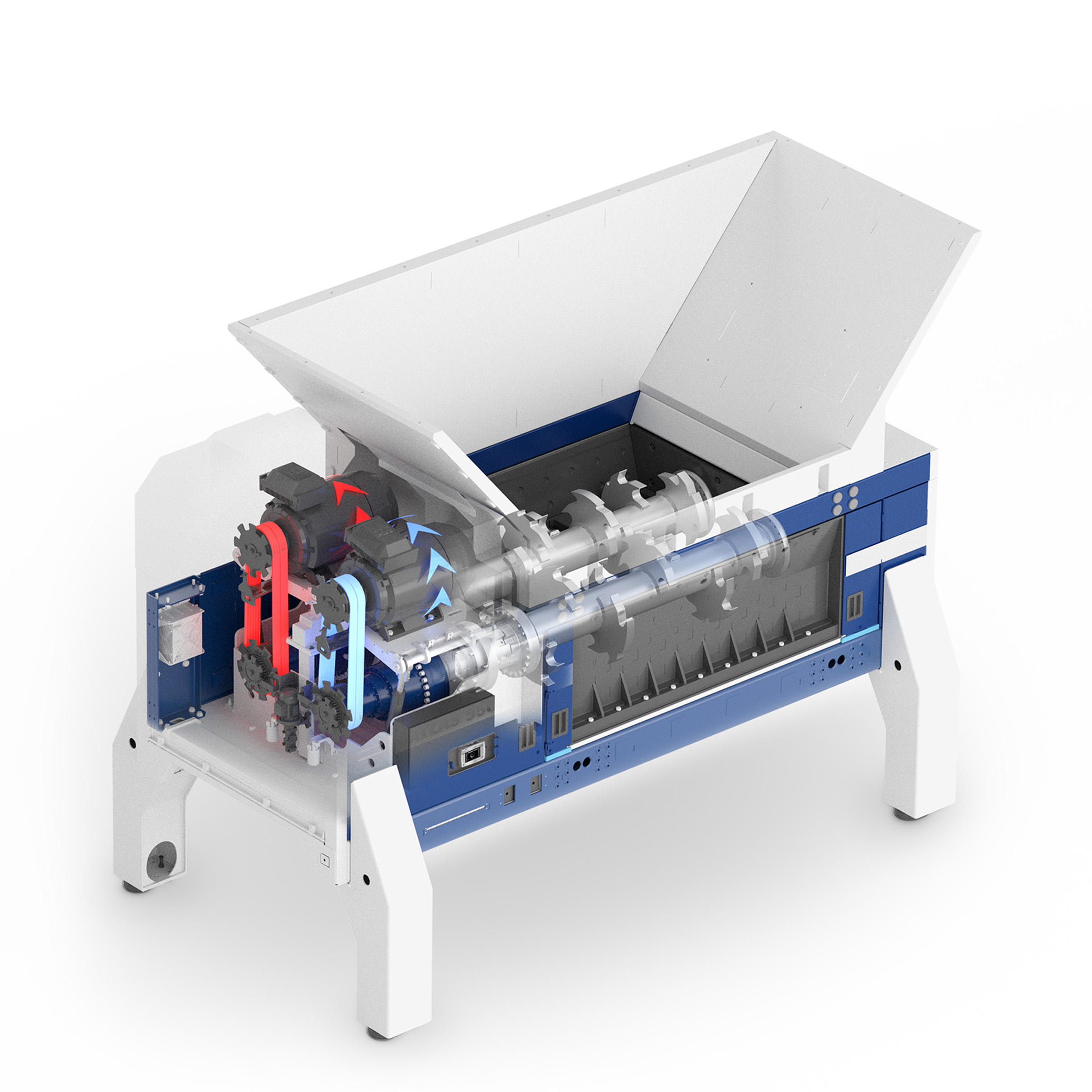
1 | Belt drive with planetary gears
Based on the proven belt concept, Lindner’s Atlas 5500 AS twin-shaft primary shredder sets new efficiency standards with its high-performance planetary gears, innovative DEX (Dynamic Energy Exchange) energy recovery system, and asynchronous shaft control.
Lindner’s ATB – automatic belt tensioning system:
- Ensures optimum power transmission at all times
- Belt exchange using a hydraulic tensioning device
- Self and preventive monitoring
Compressed air ventilation drive unit:
- Protects the drive unit from dirt
- Significantly reduced maintenance activities
- With radial fan and self-cleaning function
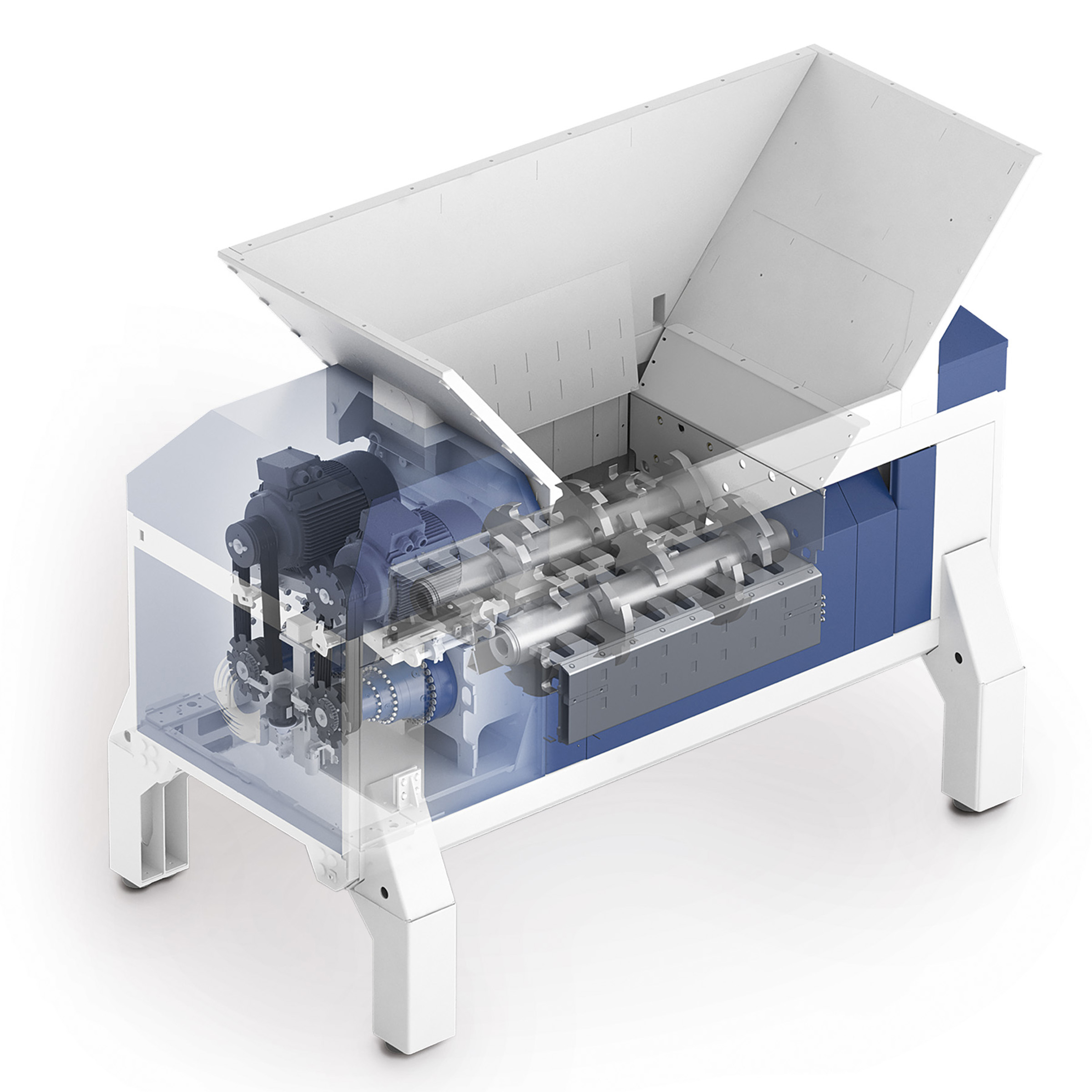
2 | DEX – Smart energy management system
LINDNER’S DEX – OUR DYNAMIC ENERGY EXCHANGE SYSTEM – FOR MAXIMUM EFFICIENCY
Maximum efficiency is achieved by actively using braking energy when reversing one of the shafts. Top productivity is ensured with an instant, power electronics-controlled reversal of the shaft running direction.
- INNOVATIVE, LOAD-DEPENDENT energy management
- HIGHEST ENERGY EFFICIENCY in operation
- MAXIMUM AGILITY while changing the running direction, up to 3 times faster
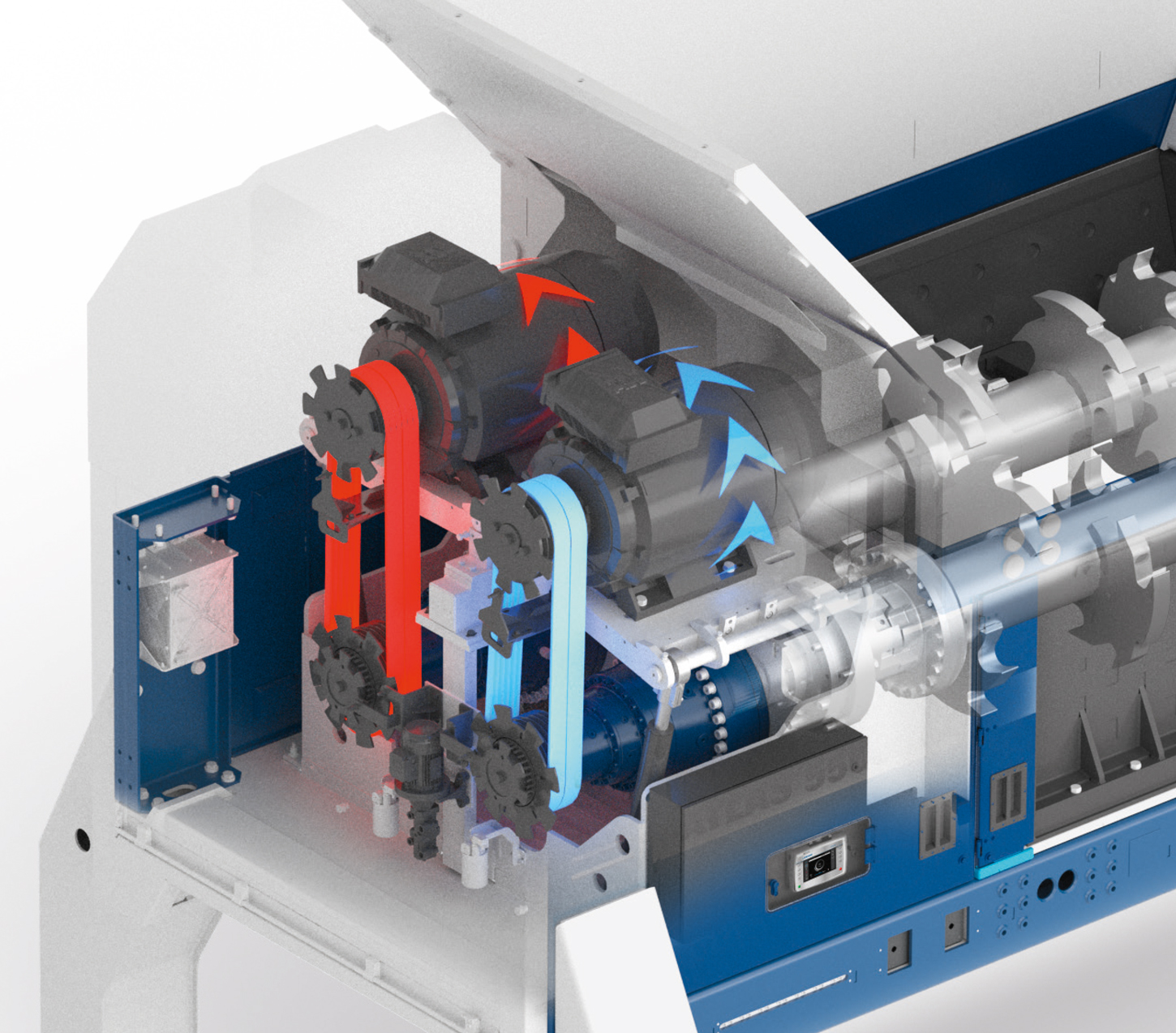
3 | Mechanical safety clutch
TORQUE-LIMITING SAFTEY CLUTCH
- OPTIMUM DRIVE PROTECTION thanks to the drive unit's instant mechanical disengagement
- SECURE POWER DOWN with our tried-and-tested sensors
- FLEXIBLE ADJUSTABILITY to the input material
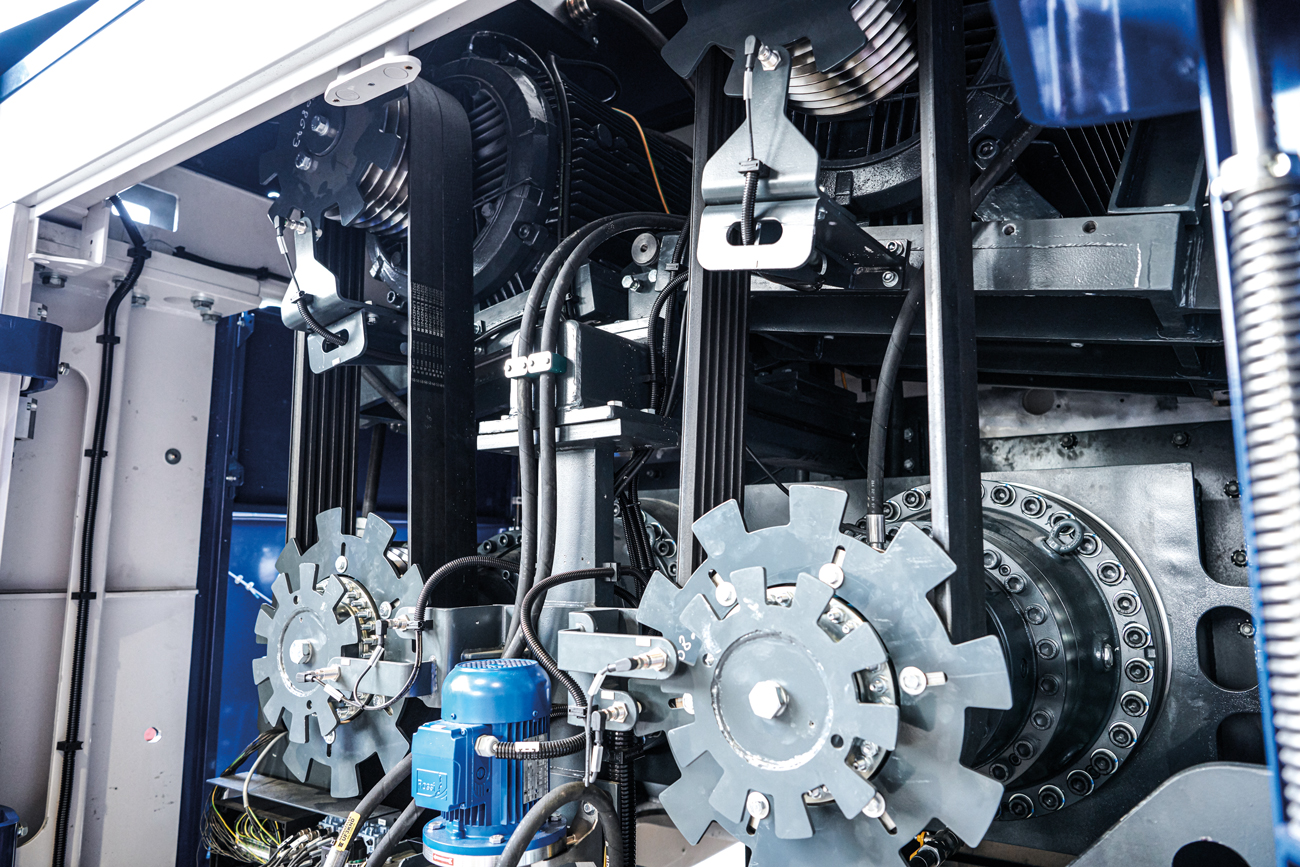
4 | Twin-shaft cutting system
The cutting system of the Atlas AS consists of two asynchronously running, fully welded rotors and a solid scraper unit. The asynchronous ripping (ripping apart, ripping up) at low speeds with high torque combined with the dynamic energy recovery enables:
- Aggressive material intake
- Continuous volume flow
- Highest productivity
- Ideal output material for sorting
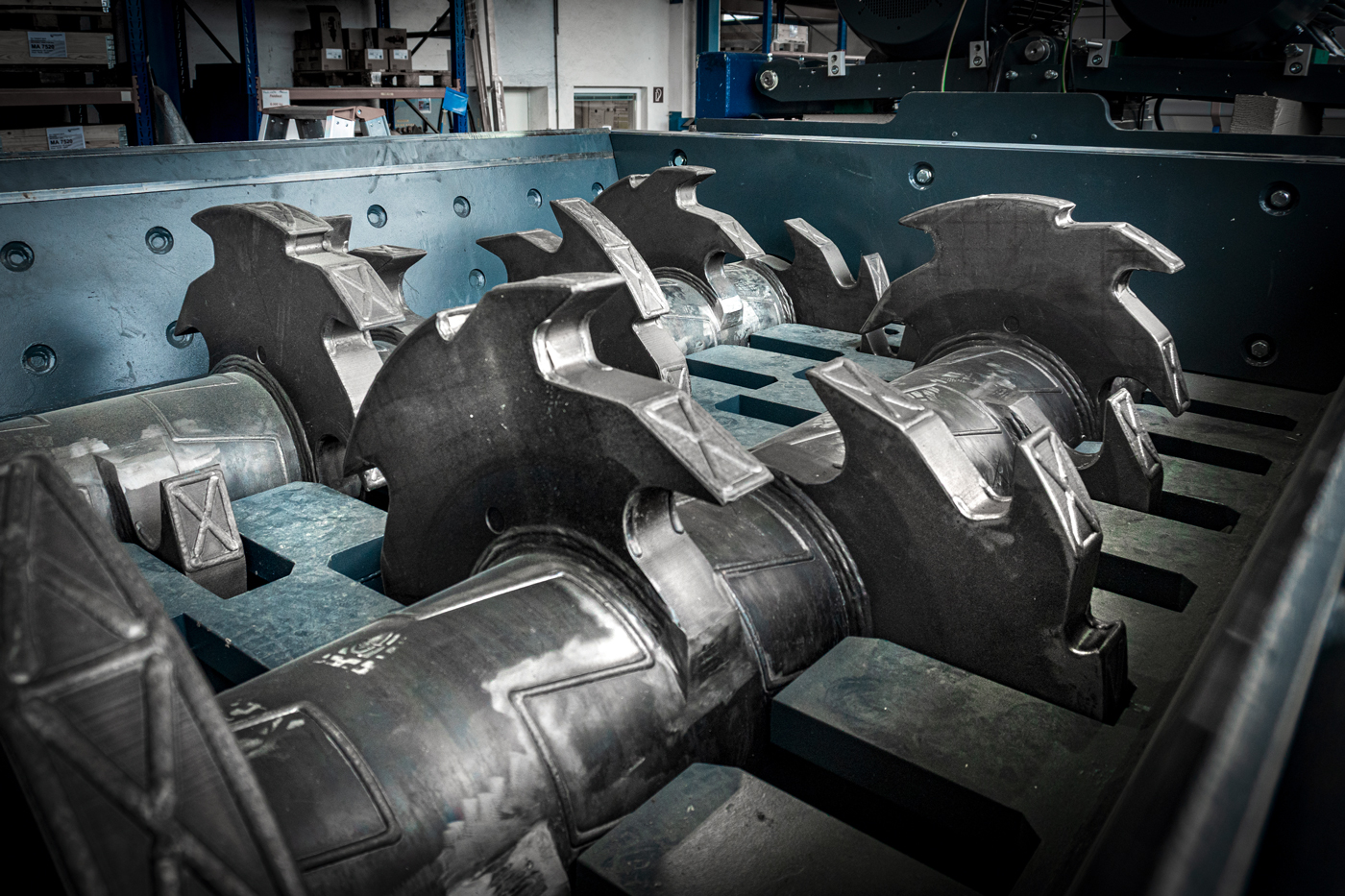
5 | FX – Fast exchange system
The Atlas series has been perfected to give you easy access to the cutting unit and provides two options for removing or changing the entire cutting unit or individual components. The components can be removed from the side via the hydraulically operated, swivelling slider or, after removal of the hopper, from the top.
- The cutting unit can be exchanged quickly, ensuring minimum downtime
- The two quick-change options guarantee maximum flexibility
- Easy and fast removal of the hopper
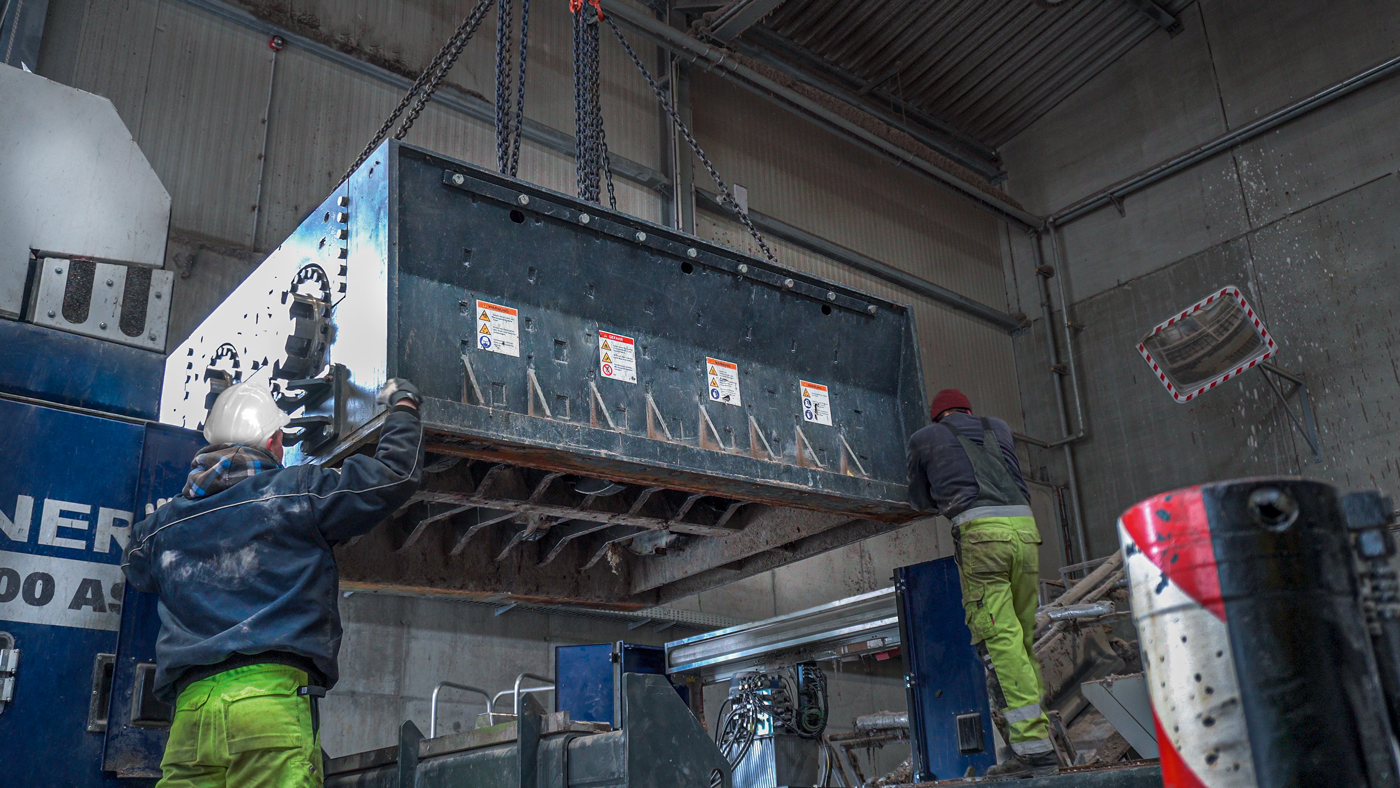
6 | Controlling & operation
- INTUITIVE MENU NAVIGATION due to software functions automatically opening and closing depending on the task at hand
- HIGH AVAILABILITY thanks to fast troubleshooting with smart solution-finding and integrated FAQ database
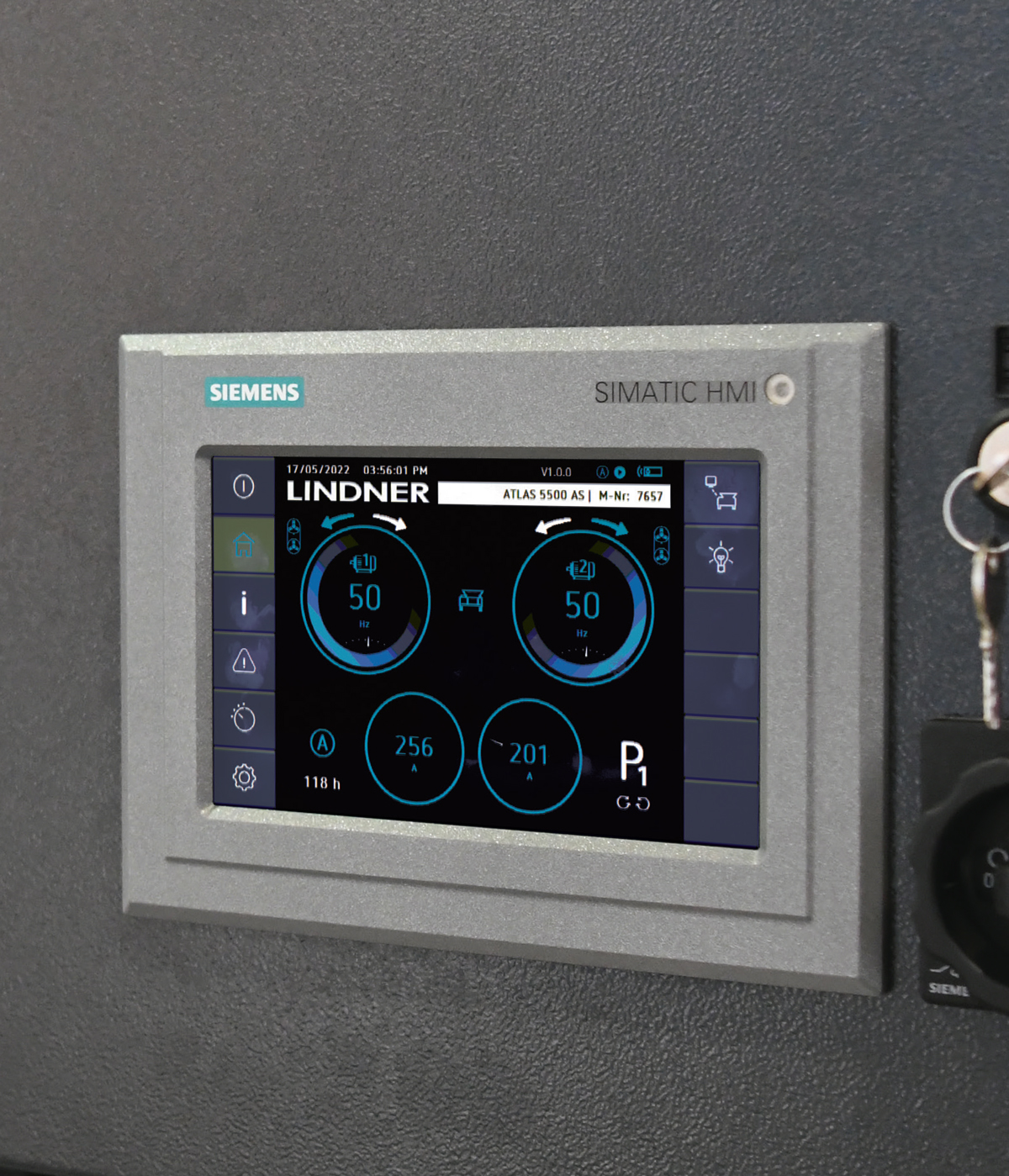
Fire prevention
THAT’S HOW TO PLAY IT SAFE
Lindner’s modern out-of-the-box FPS solution automatically detects and cools over heated particles in the material stream directly on the discharge conveyor, effectively preventing possible sources of fire. The system adapts the cooling process to the hazardous situation to ensure the facility operates optimally at all times.
- Precise detection of overheated materials
- Comprehensive monitoring of the entire cooling section
- Cooling process adapted to the hazardous situation
- Independent cleaning of the infrared sensors
- Temperature resistant and robust thanks to a special insulation system
- Highly flexible modular design
Watch video here!
Water sprinkling system
- To remove dust from the filling area
- 4 spray nozzles positioned in the enclosed hopper
- Switch it ON/OFF using the control panel
- Machine piping incl. central water supply
- Incl. heating system & piping insulation
Autom. belt tensioning
Lindner ATB – automatic belt tensioning system
- Ensures optimum power transmission at all times
- Belt exchange using a hydraulic tensioning device
- Self and preventive monitoring
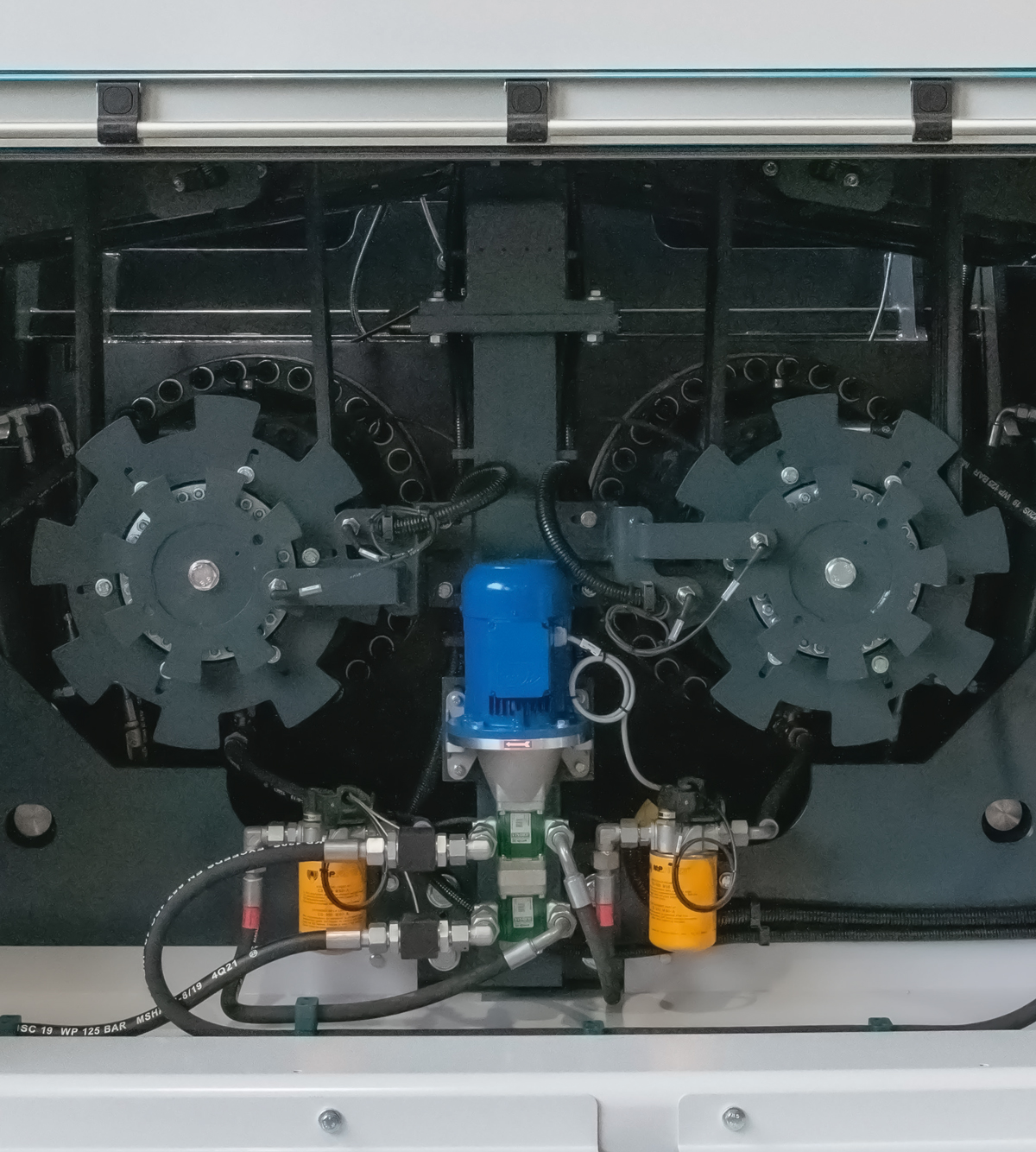
Hardfacing kit
ADDITIONAL WEAR PROTECTION PACKAGE CUTTING SYSTEM
- Ideal for shredding particularly abrasive material
- Knife hardfacing
- Scraper hardfacing
Fast exchange system
OUR UNIQUE FAST EXCHANGE SYSTEM (FX)
The Atlas series has been perfected to give you easy access to the cutting unit and provides two options for removing or changing the entire cutting unit or individual components. The components can be removed from the side via the hydraulically operated, swivelling slider or, after removal of the hopper, from the top.
- The cutting unit can be exchanged quickly, ensuring minimum downtime
- The two quick-change options guarantee maximum flexibility
- Easy and fast removal of the hopper
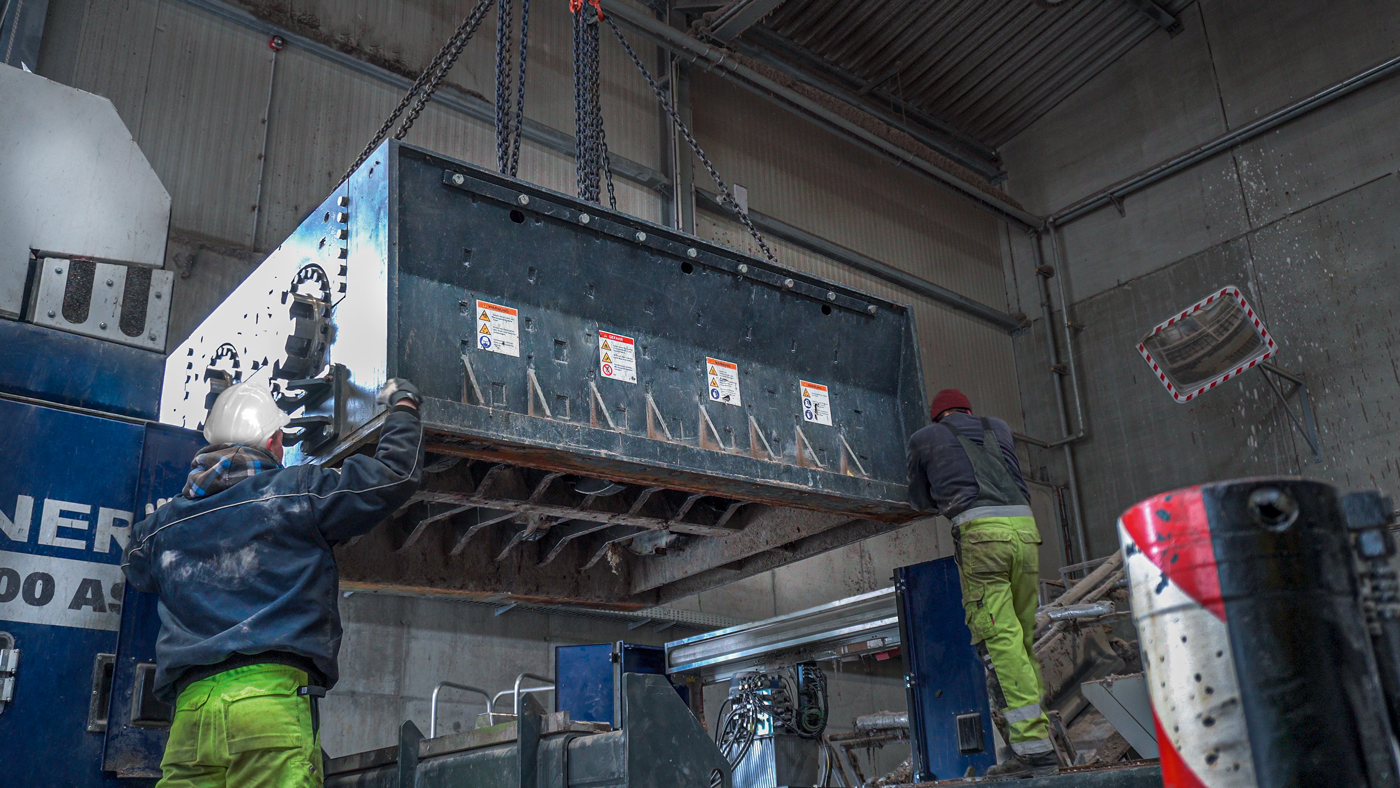
Find your ideal solution and
Connect with us
INPUT & OUTPUT MATERIALS
MSW
MSW PLASTICS
C&I WASTE
KEY FEATURES
LINDNER ADVANTAGES
Resources
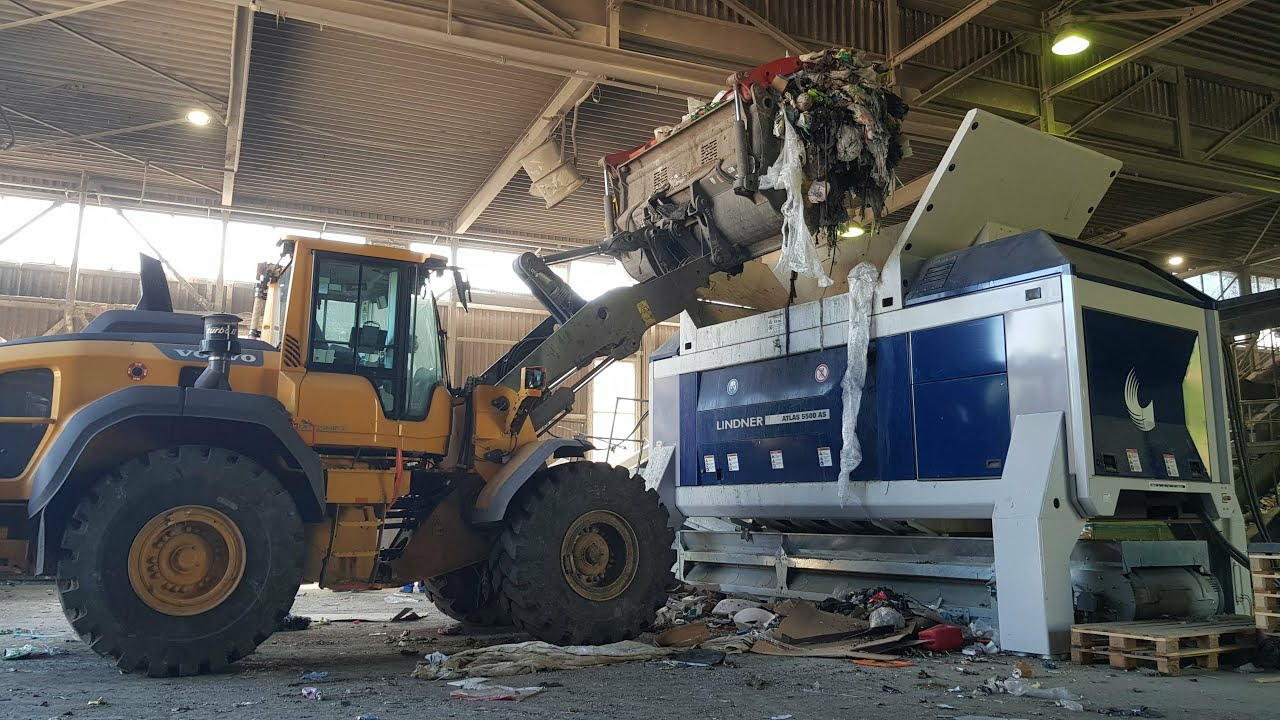
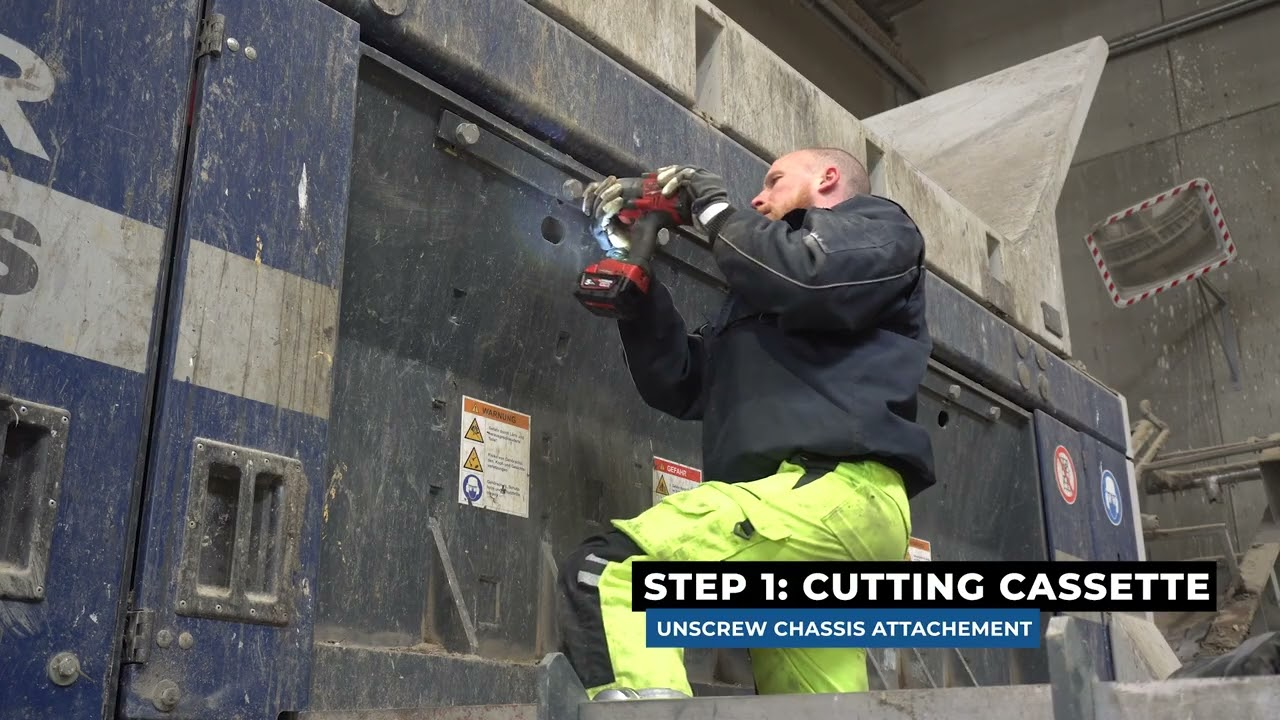
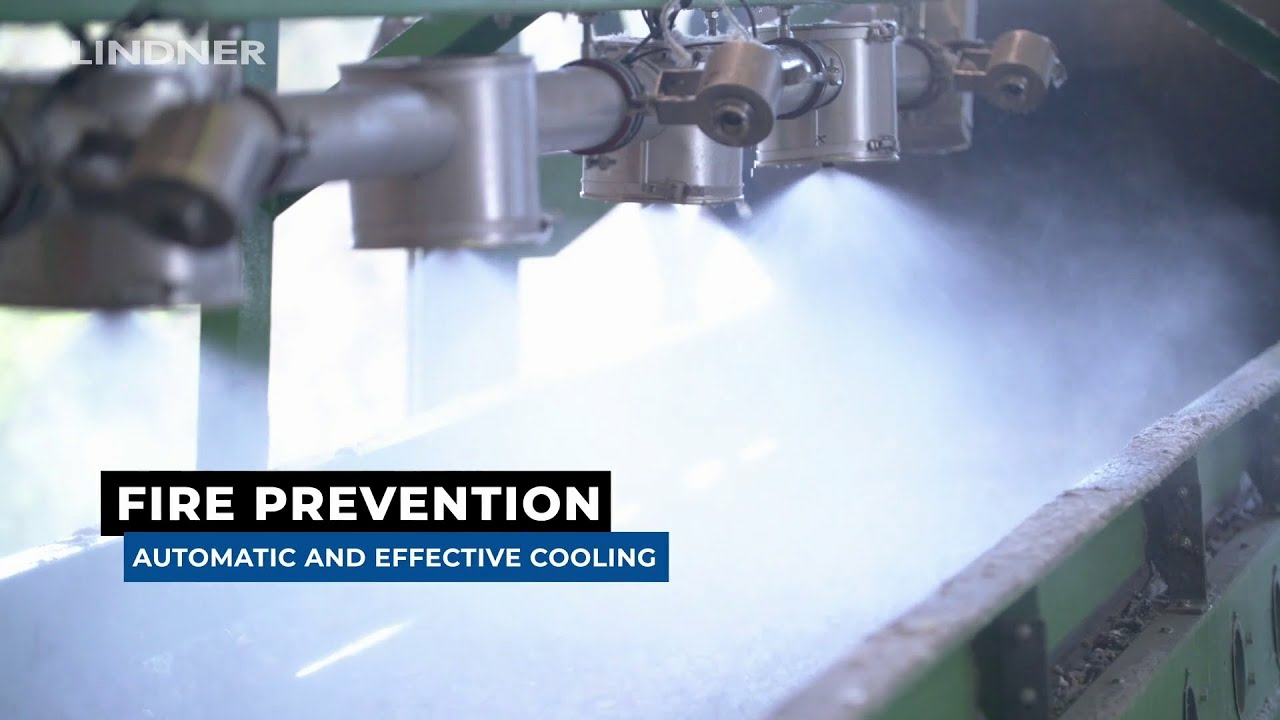
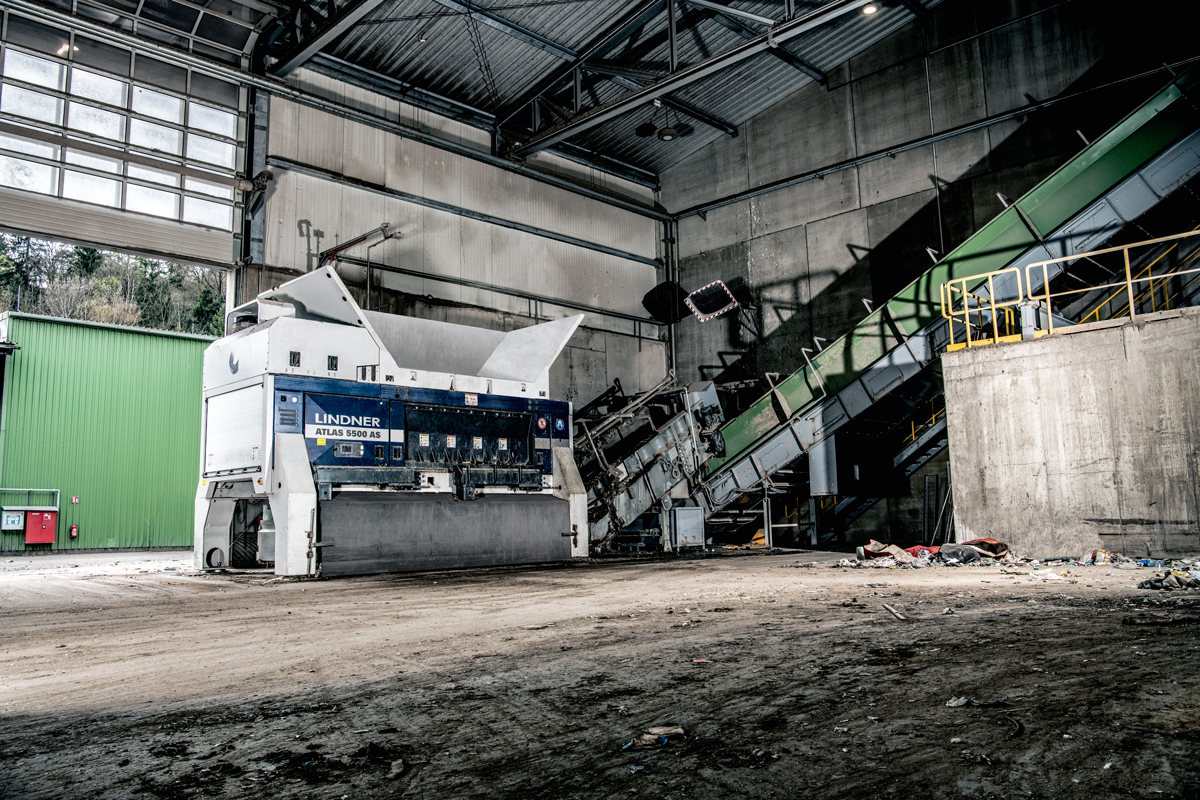
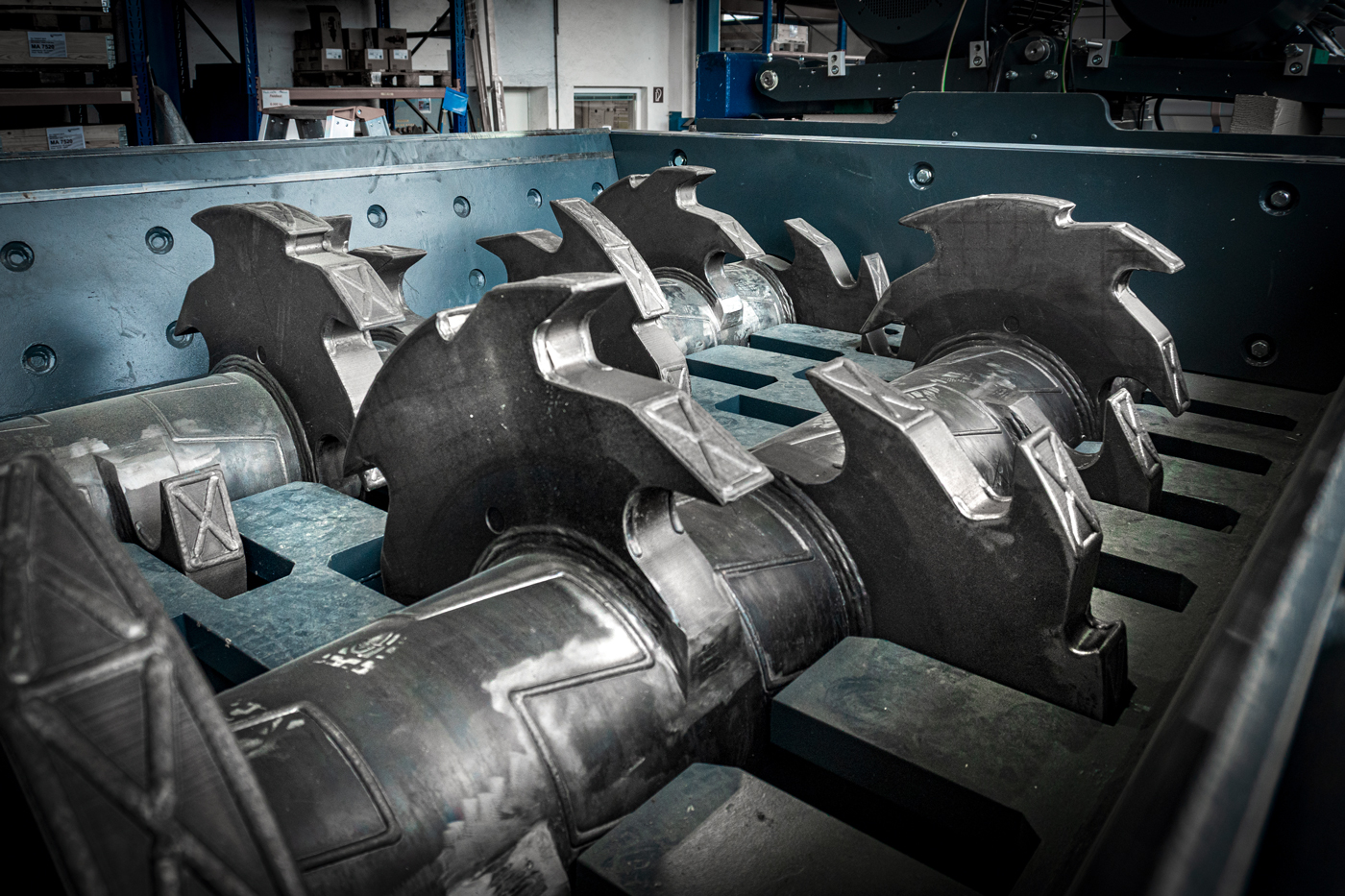
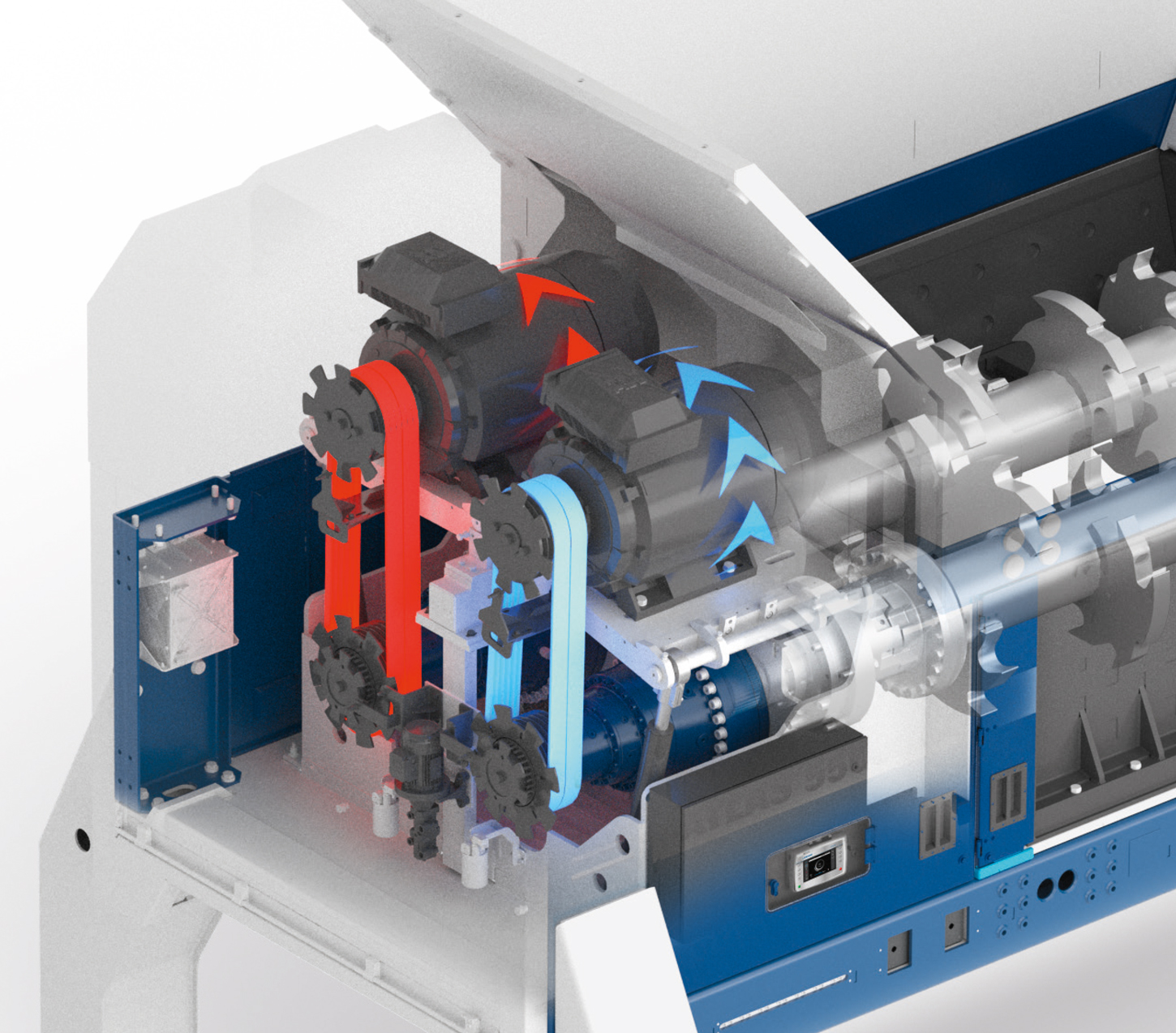
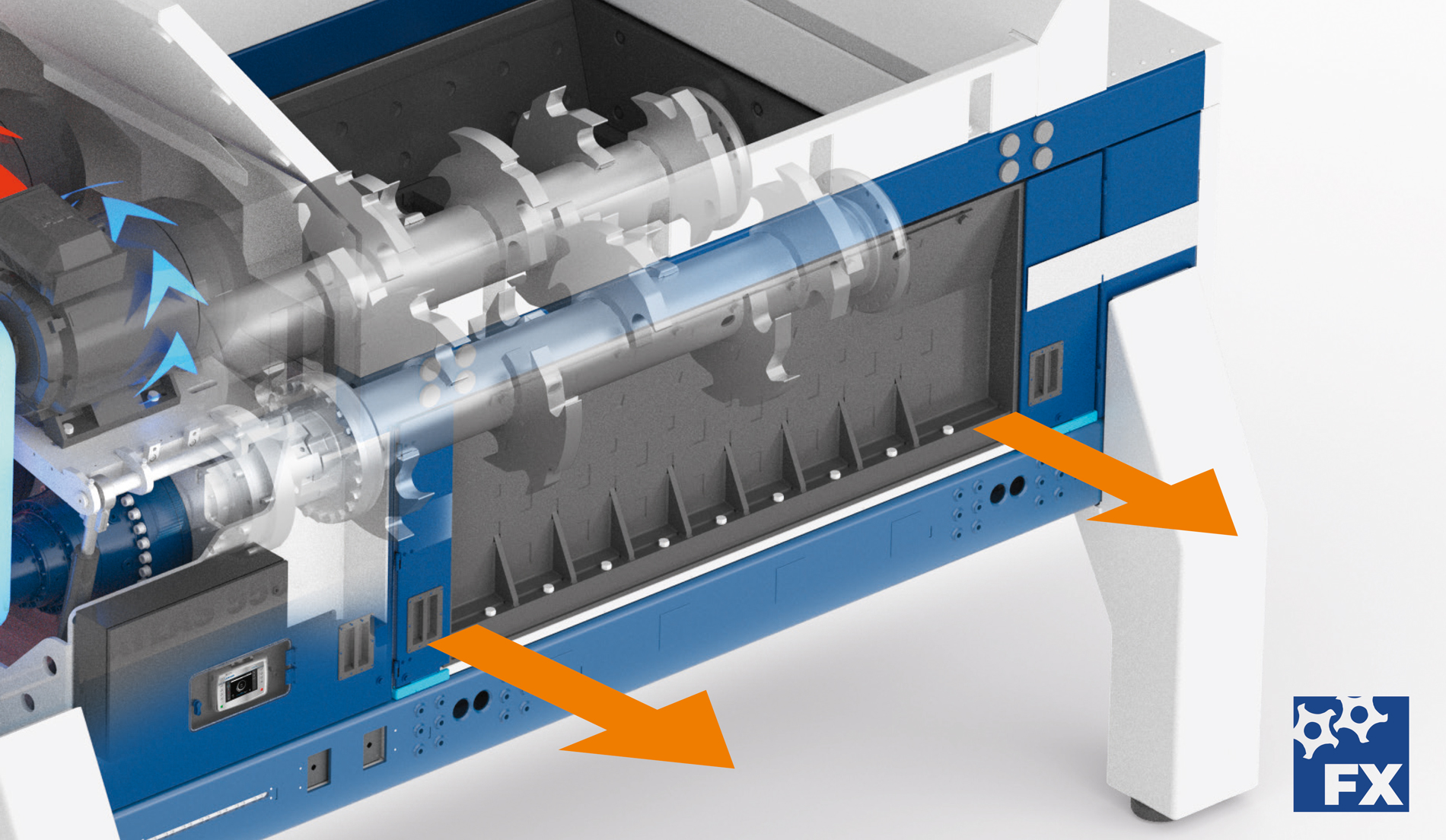
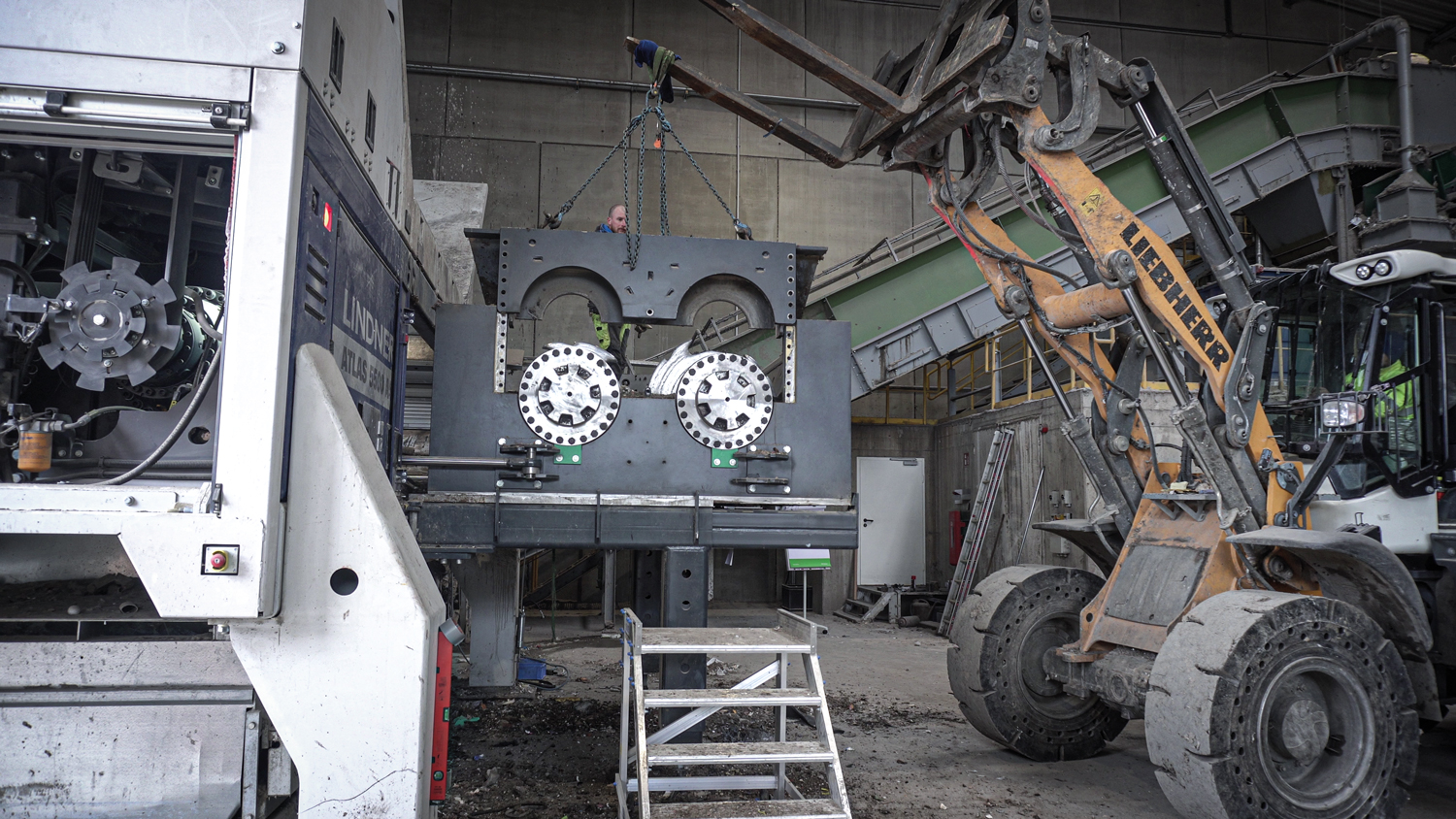
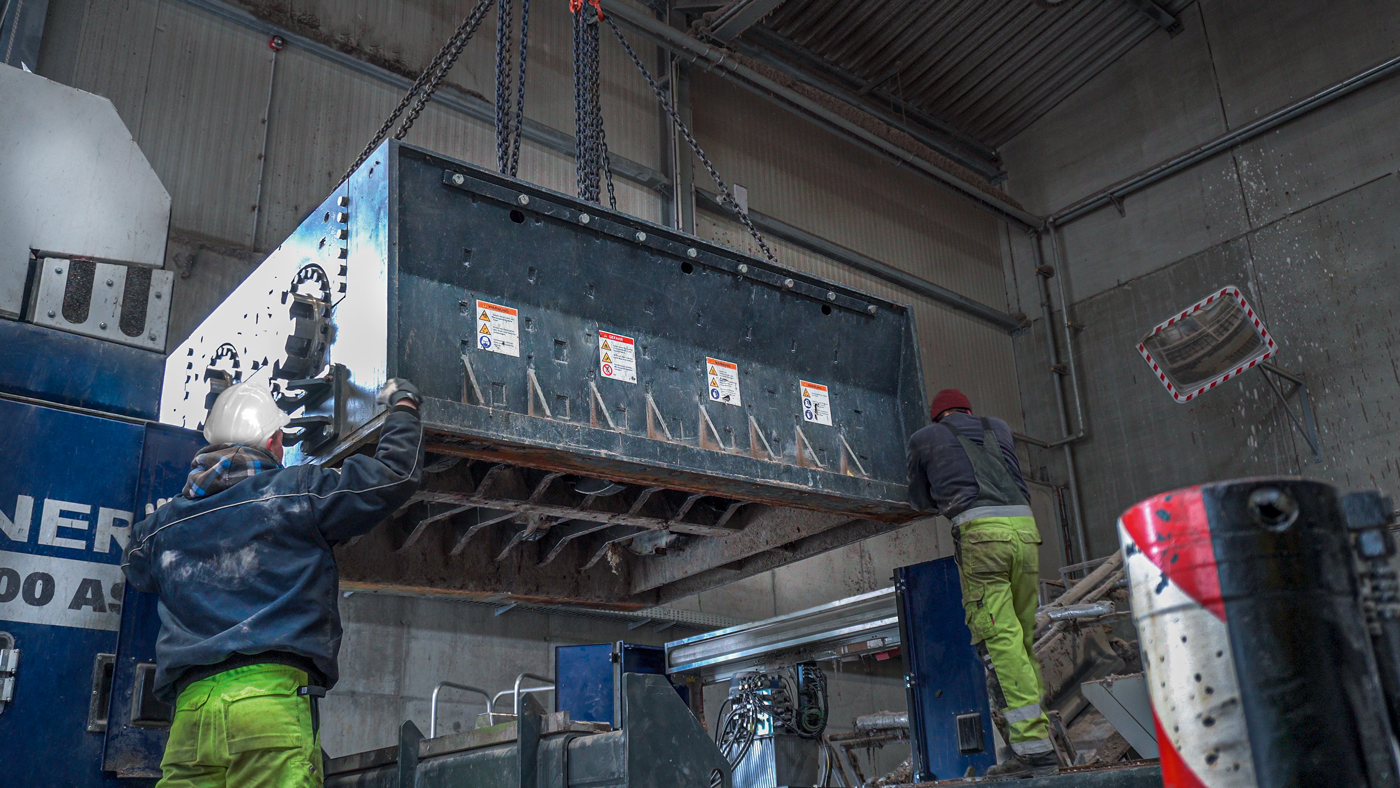
| ATLAS 5500 AS | |
Dimensions* | ||
Measure (LxWxH) | mm | 6150 x 3390 x 4810 |
Hopper opening (DxF) | mm | 5470 x 2230 |
Feeding height (G) | mm | 3310 |
Hopper capacity | m³ | 18 |
Outlet width (I) | mm | 1510 |
Total weight | kg | 35000 |
Cutting unit* | ||
Rotor length | mm | 2 x 2380 |
Rotor speed | min-1 | 36 |
Asynchronous twin-shaft cutting system | AS 4.8 | AS 4.12 | |
Drive unit* | ||
Motor | kW | 2 x 110 |
Frequency converter | ✔ |
* The stated values refer to standard machine versions with a standard hopper (large) and raised feet.