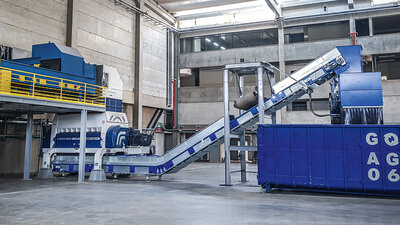
KOMET 2200 HP | 2800 HP
Unbashedly Strong.
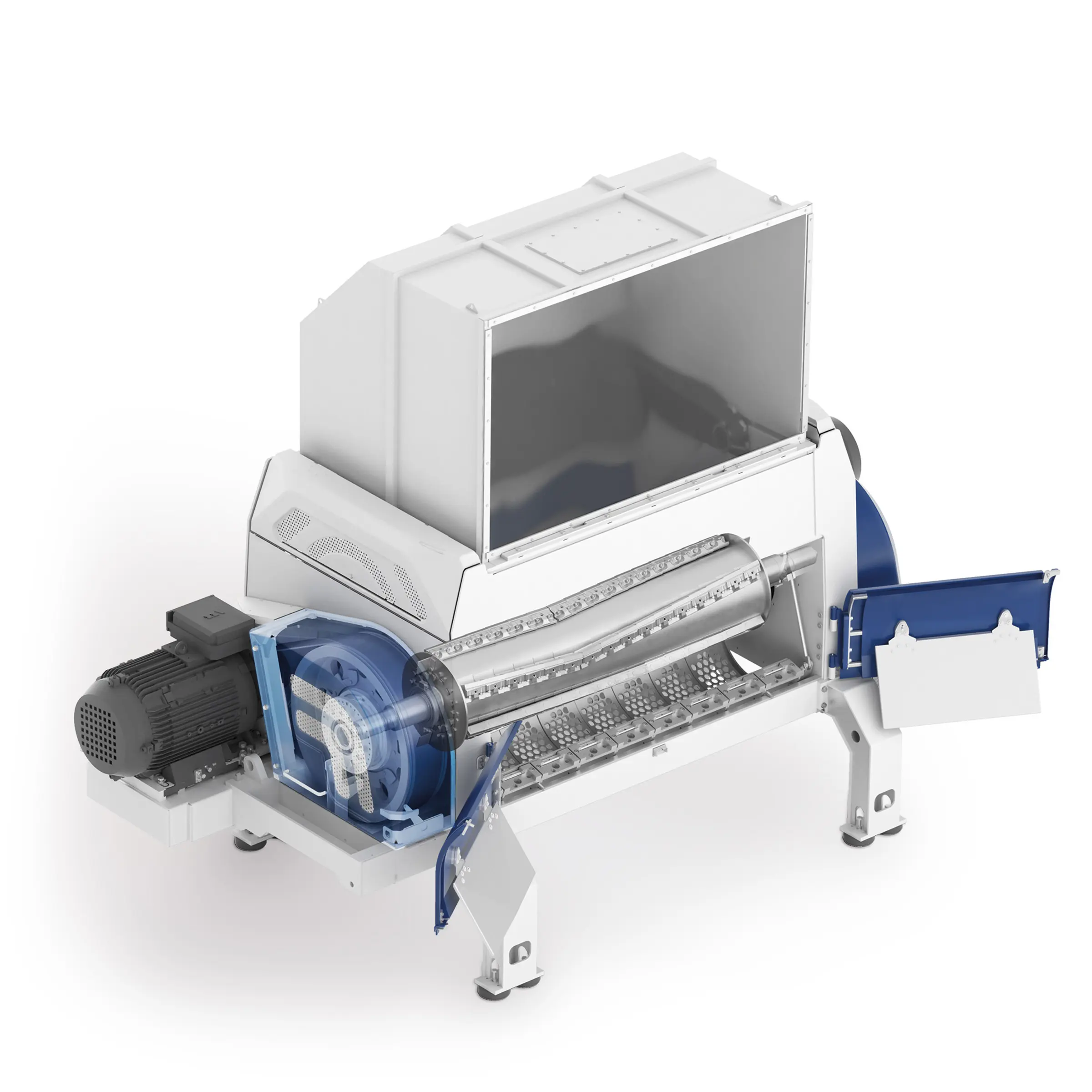
Find Your Ideal Solution And
Connect With Us
Need answers about applications or particle sizes? Reach out today - our specialists are ready to provide support. Together, we'll uncover your perfect solution.
Input & Output Materials
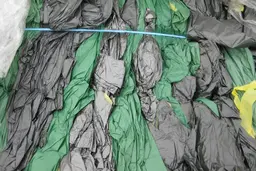
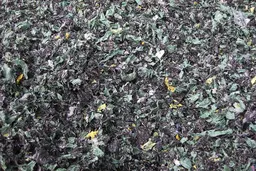
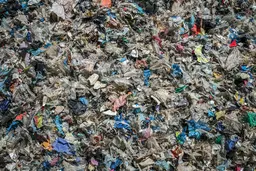
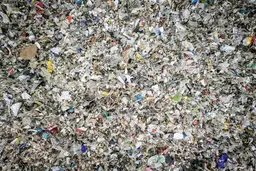
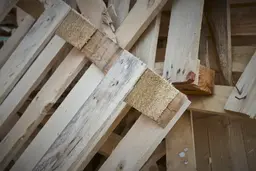
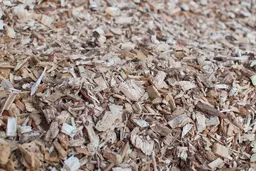
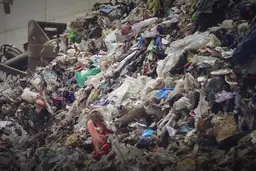
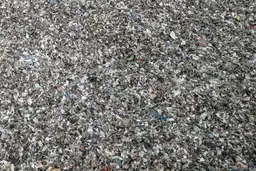
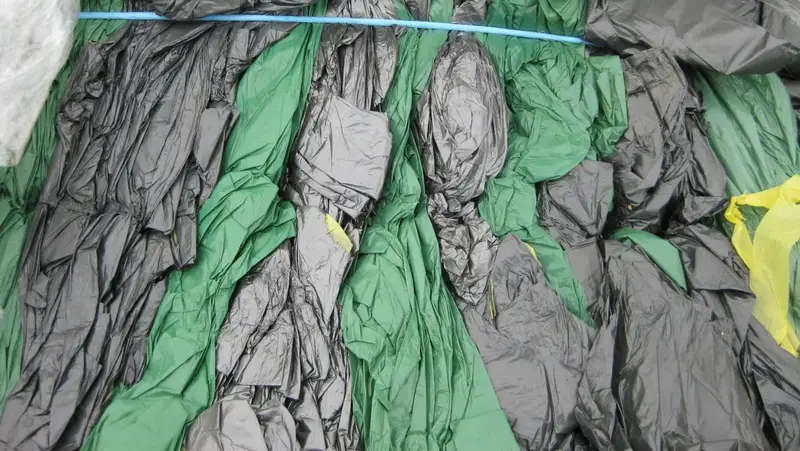
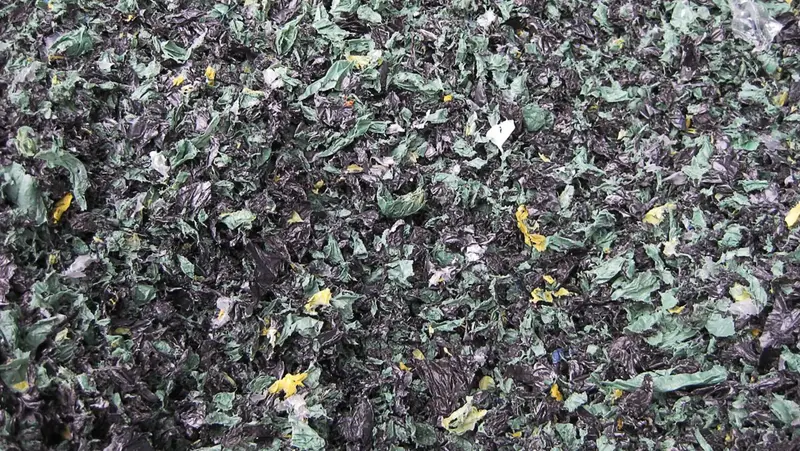
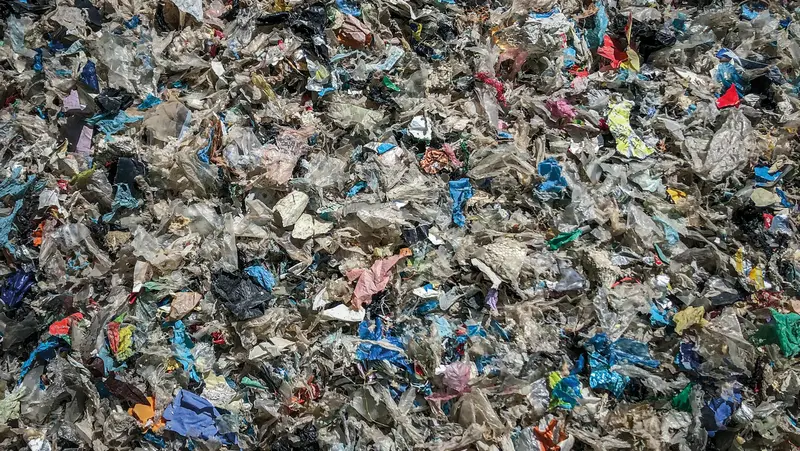
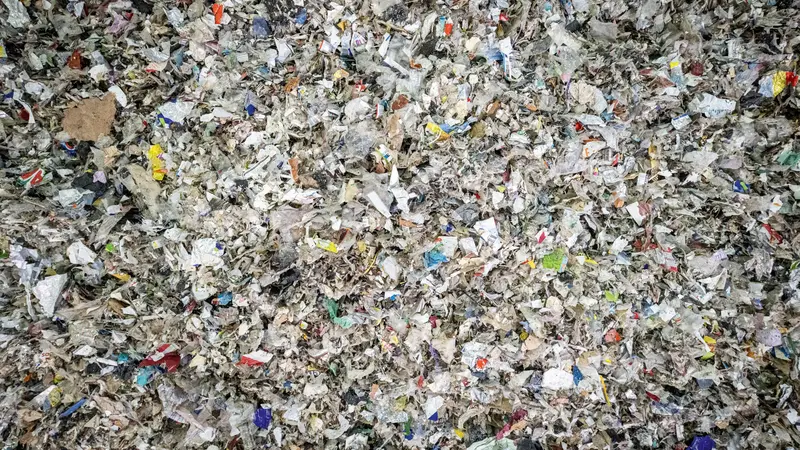
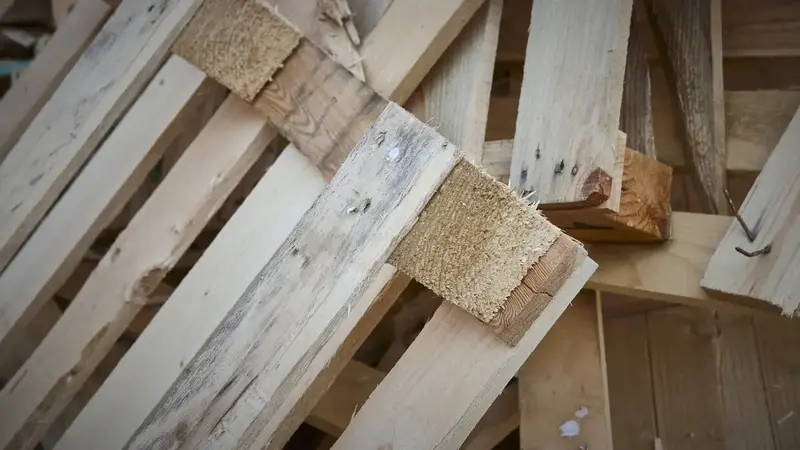
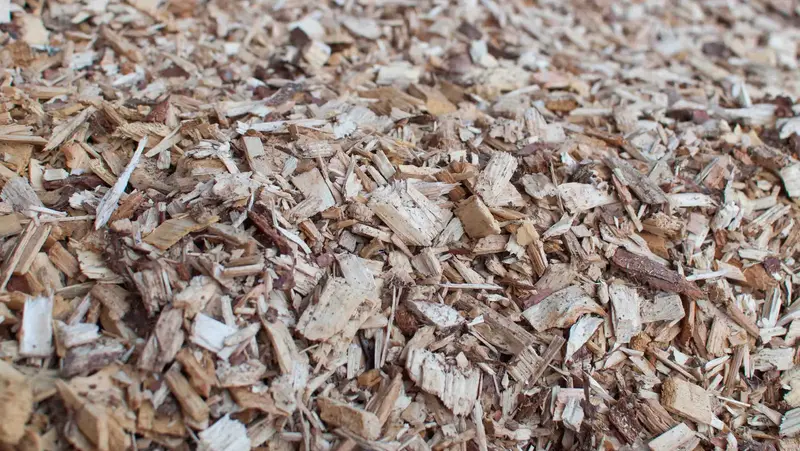
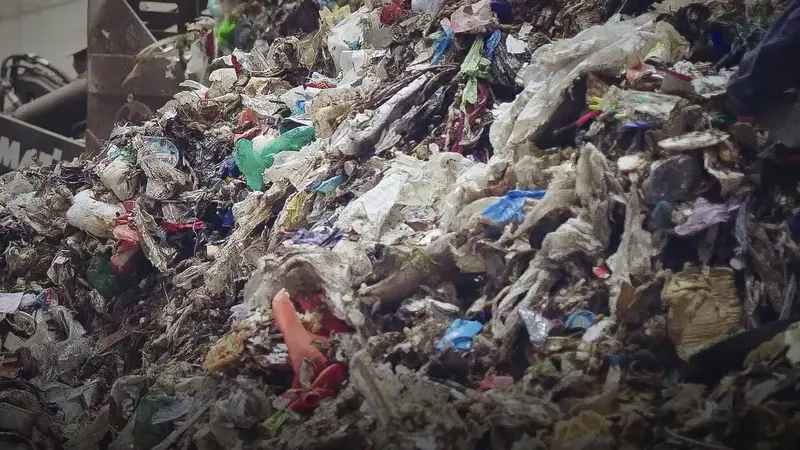
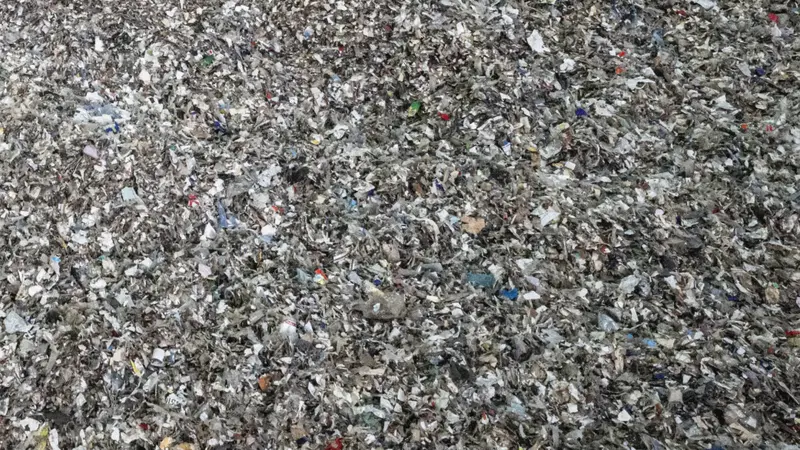
Key Features
Lindner Advantages
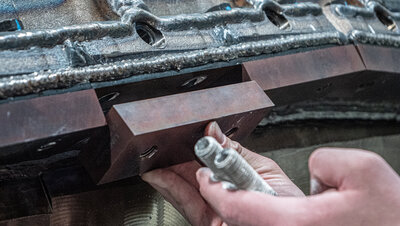
Precise Rotor with Square Knives
- High throughputs guaranteed thanks to the strategically positioned knife rows
- Consistent particle size with a cutting gap that is fully adjustable even during operation
- Optimised wear parts storage thanks to identical knives for the rotor, counter knives and scraper
- Maximum uptimes ensured by four-fold usable, quick-change knives
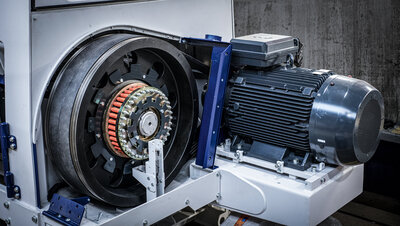
Tried-And-Tested Belt Drive
- Efficient, robust and gearless belt drive
- More output with high-performance ABB motors
- Worldwide availability of easy-to-change standard components
- Mechanical safety clutch for maximum resistance to non-shreddables
- Optional: Comfort function for automatic belt tensioning