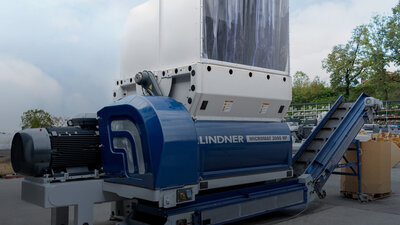
Ingeniously Productive.
The Specialist For Supreme Quality.
Single-shaft shredder with direct belt drive, unique Mono-Fix technology and lightning-fast safety clutch: this formula makes the Micromat HP series the benchmark for individual and flexible shredding of post-consumer and post-commercial plastics. The gearless drive of the Micromat HP series ensures continuously high throughputs at high speeds and, thanks to Lindner’s safety clutch, maximum protection against non-shreddables.
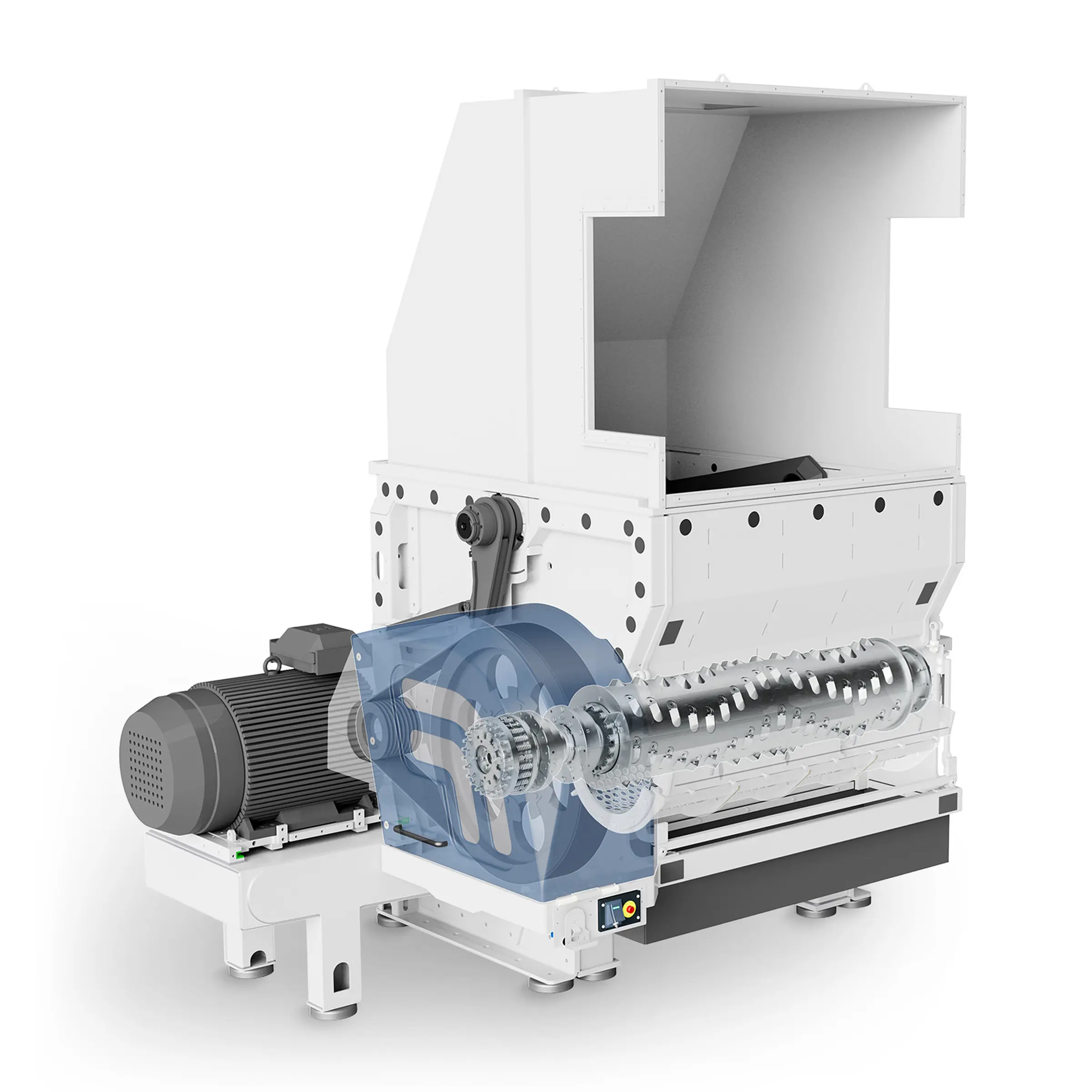
Connect With Us
Need answers about applications or particle sizes? Reach out today - our specialists are ready to provide support. Together, we'll uncover your perfect solution.
Input & Output Materials
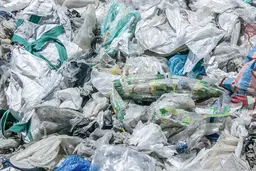
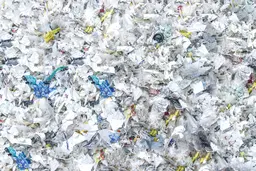
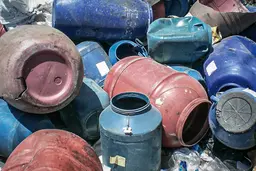
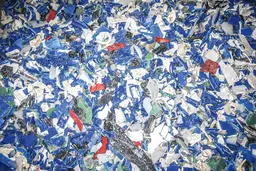
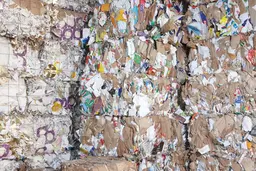
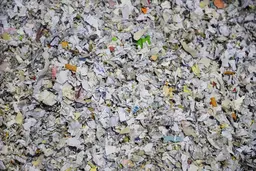
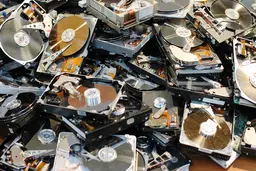
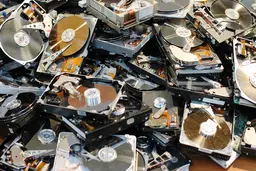
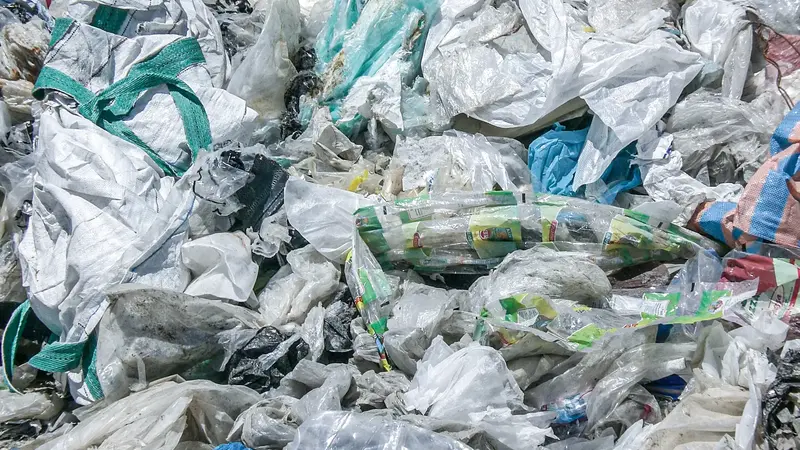
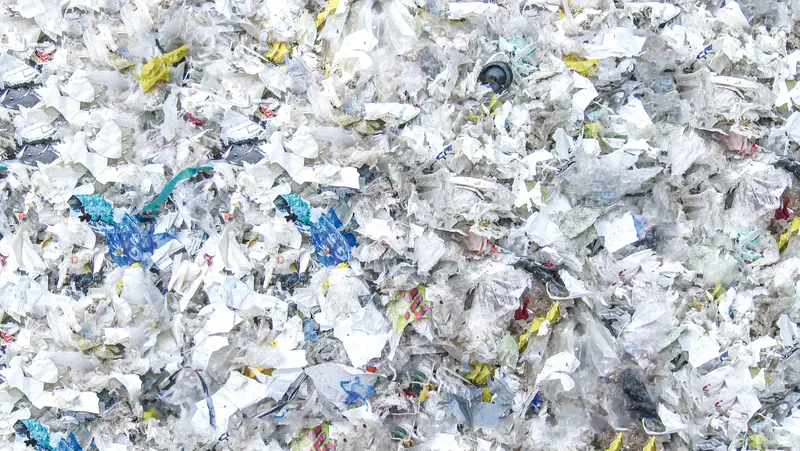
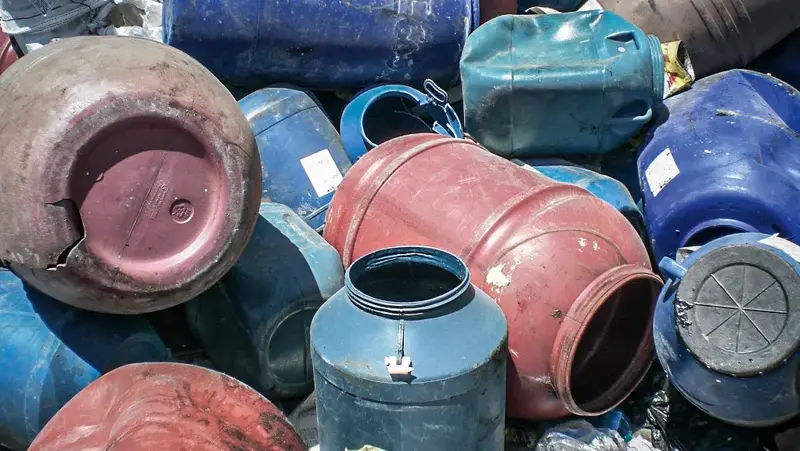
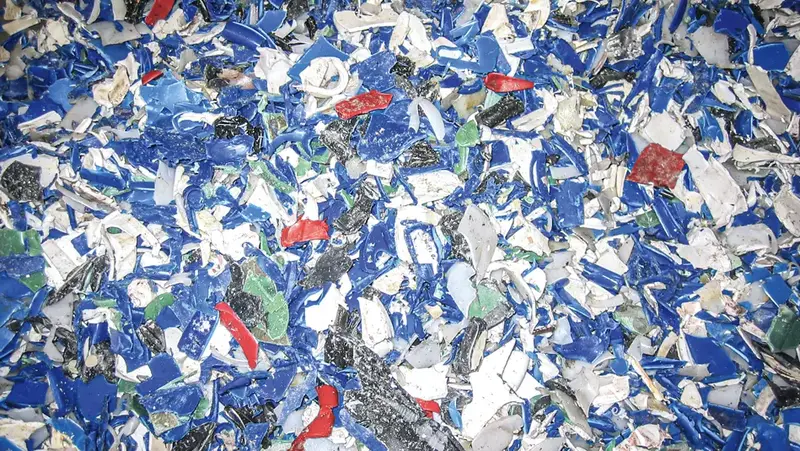
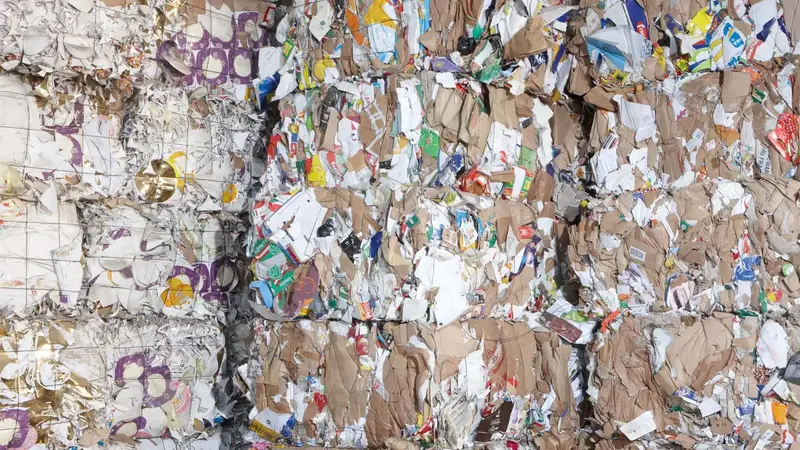
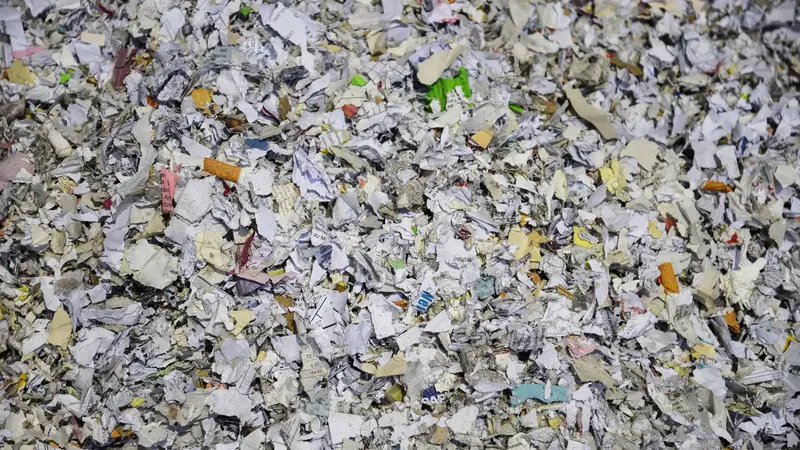
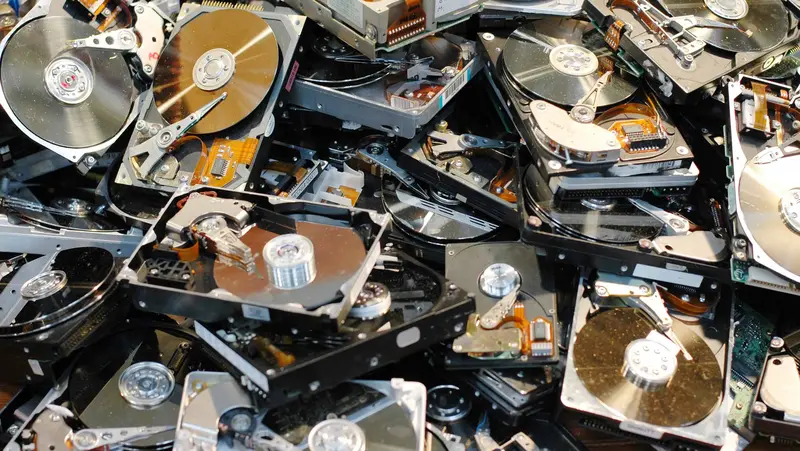
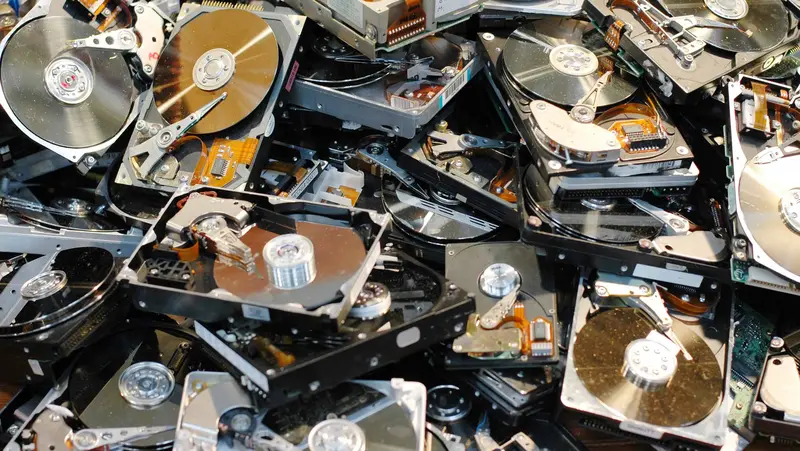
Lindner Advantages

High Performance Belt Drive
Powerful motors and an efficient, gearless direct belt drive: this formula makes the single-shaft shredders of the Micromat HP series the new standard for the shredding of post-consumer or post-commercial plastics:
- Powerful shredding thanks to high-performance, high-torque motors
- Lightning-fast safety clutch provides optimum‚ machine protection
- Worldwide availability of easy-to-change machine components
- Optional: Comfort-Function for automatic belt tension
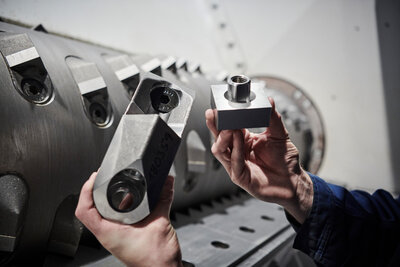
Adjustable Knife System
Knives and knife holders are easy to change thanks to the screw fitting. The knives of the 65P series are exceptionally robust as well as offering exceptionally accurate cutting. All knives of the Micromat HP series can be used 4 times and exchanged easily.
- Incredibly solid and robust
- Continuous cut quality
- Low maintenance due to the bolted knives and knife holder