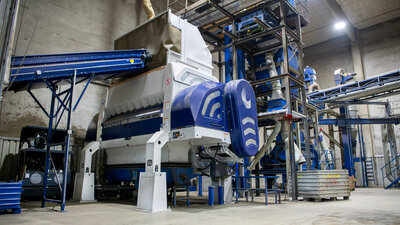
Goes It Alone.
Cost-Efficient, Highly Reliable And Only One Step.
Nothing can withstand the enormous power of the Lindner Polaris single-shaft shredder. Made for one-step processing of untreated municipal, industrial and commercial waste to obtain mid-calorific fuels (40 - 120 mm) ideal for co-incineration in calciners at cement works. Sturdy design and low operating costs are the hallmarks of this highly specialised shredder: enjoy uninterrupted shredding excellence 24 hours a day, seven days a week. With maximum efficiency throughout, as demonstrated by a field test: thanks to the countershaft drive, the Lindner Polaris shreds twice as much material as comparable machines in the same period of time.*
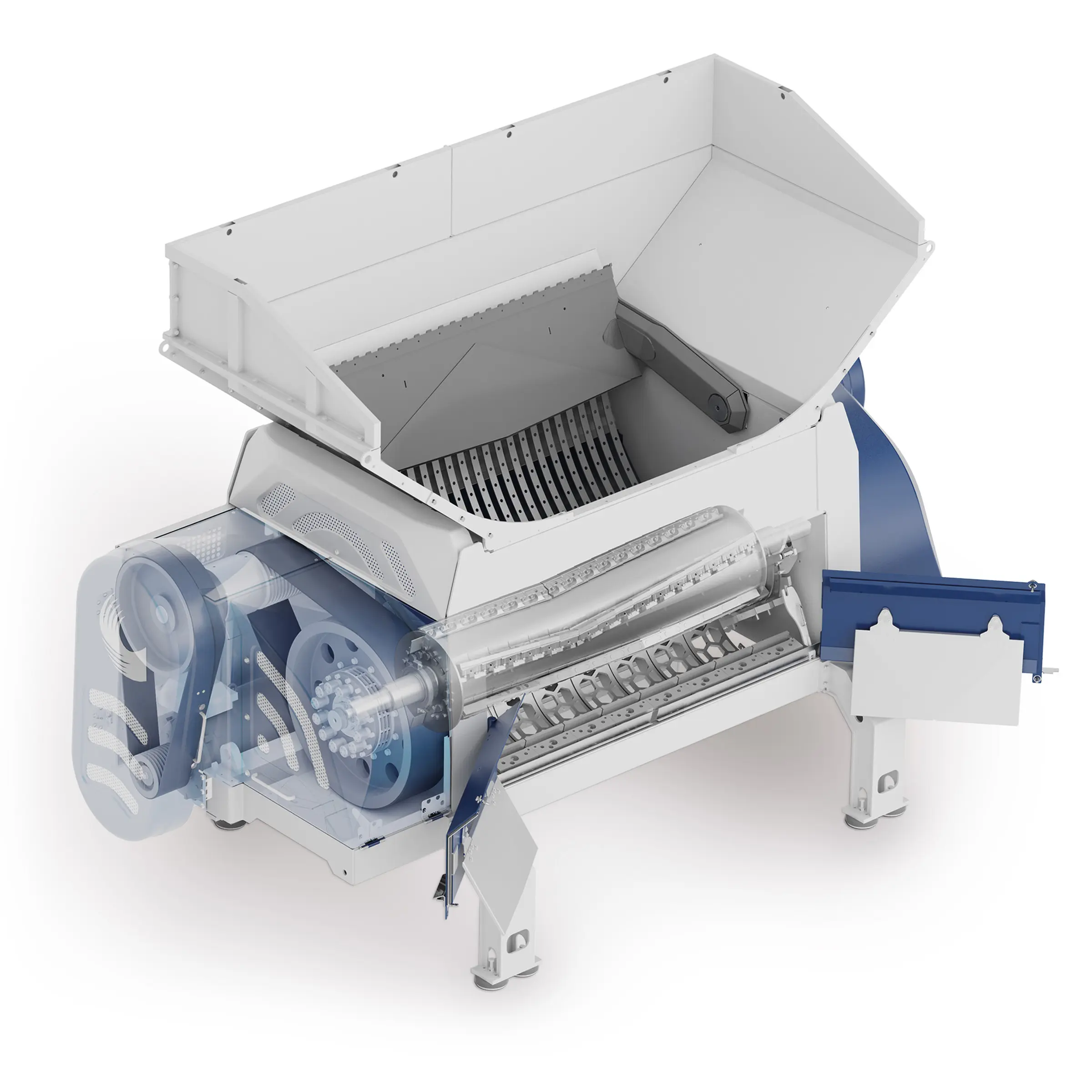
Connect With Us
Need answers about applications or particle sizes? Reach out today - our specialists are ready to provide support. Together, we'll uncover your perfect solution.
Input & Output Materials
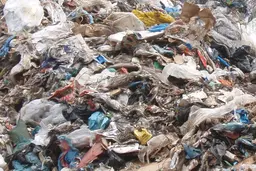
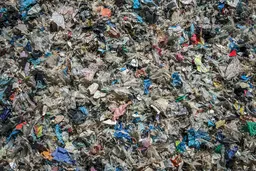
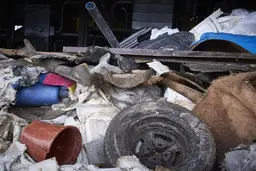
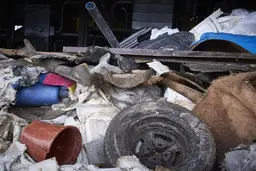
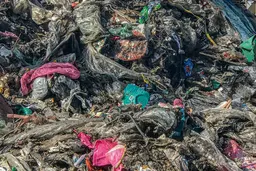
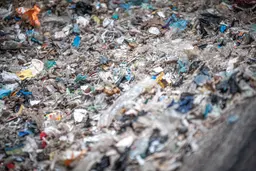
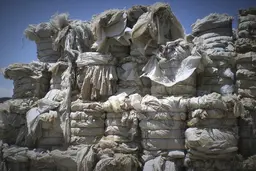
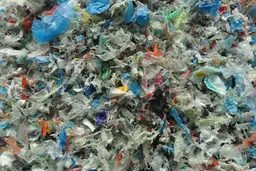
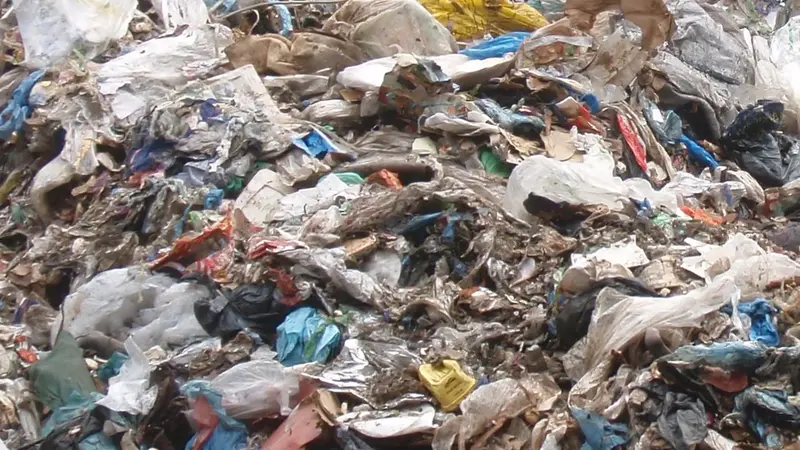
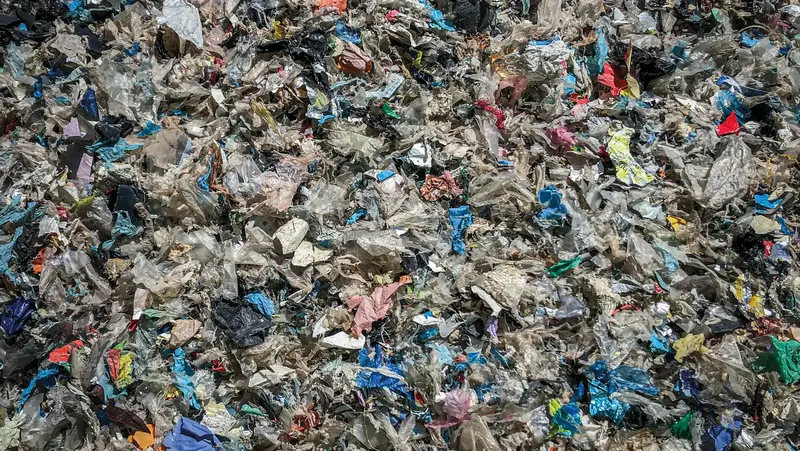
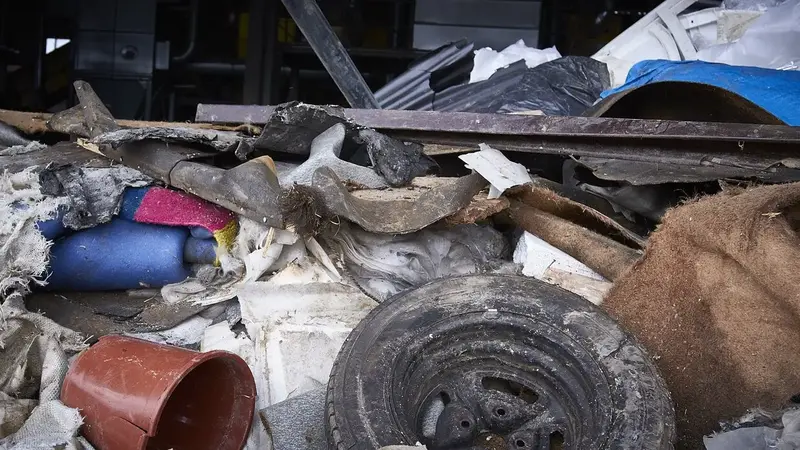
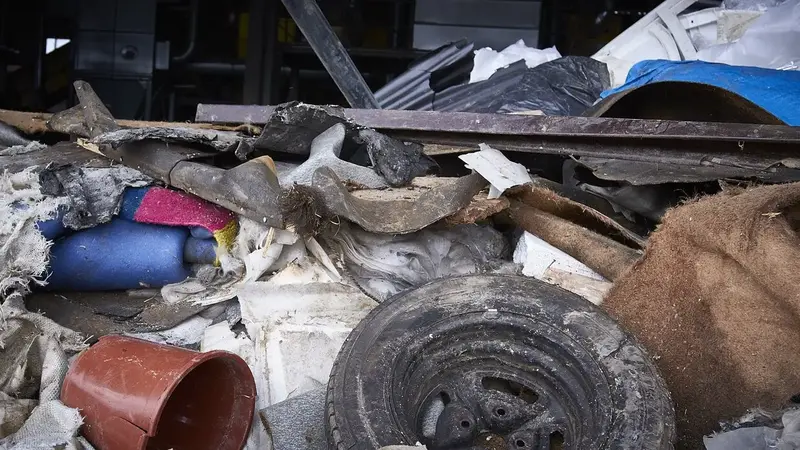
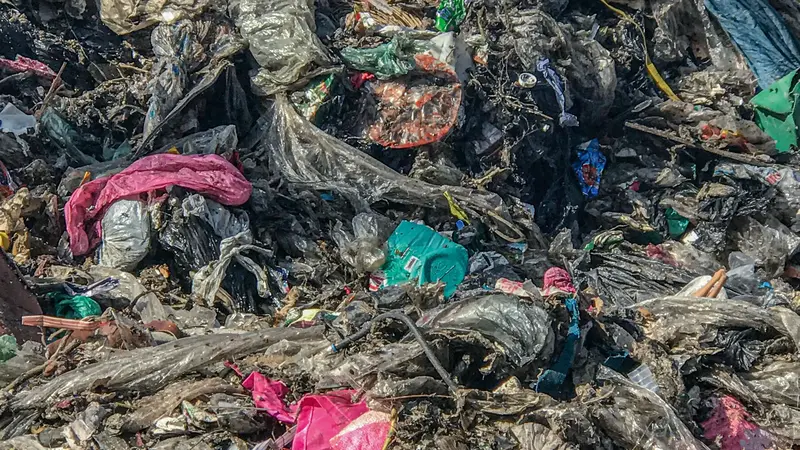
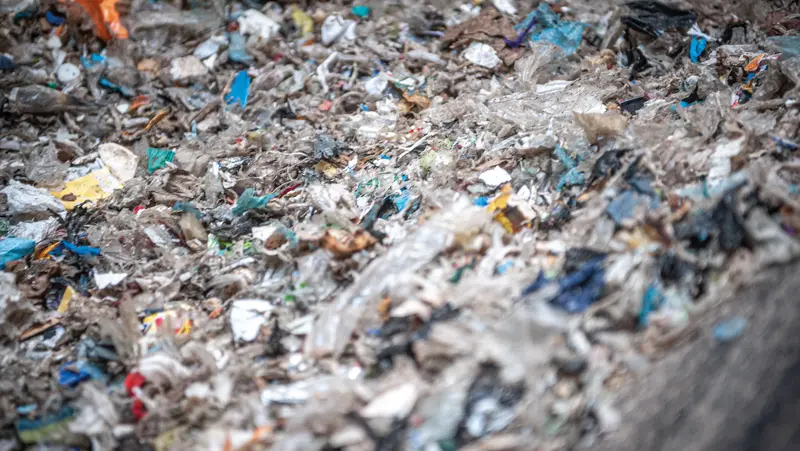
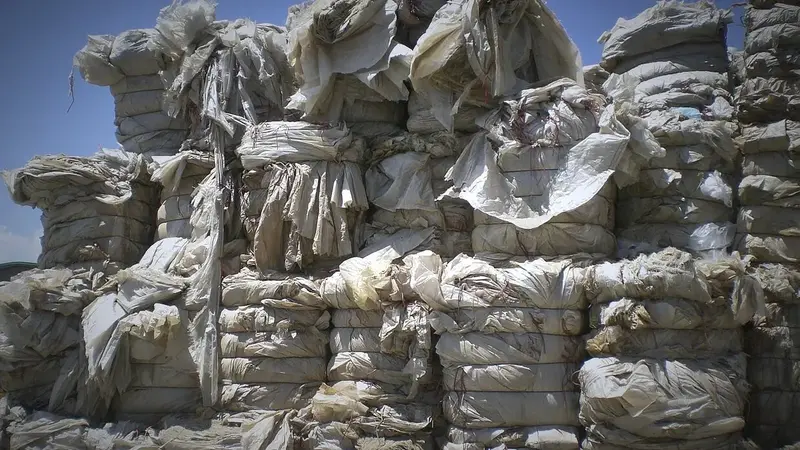
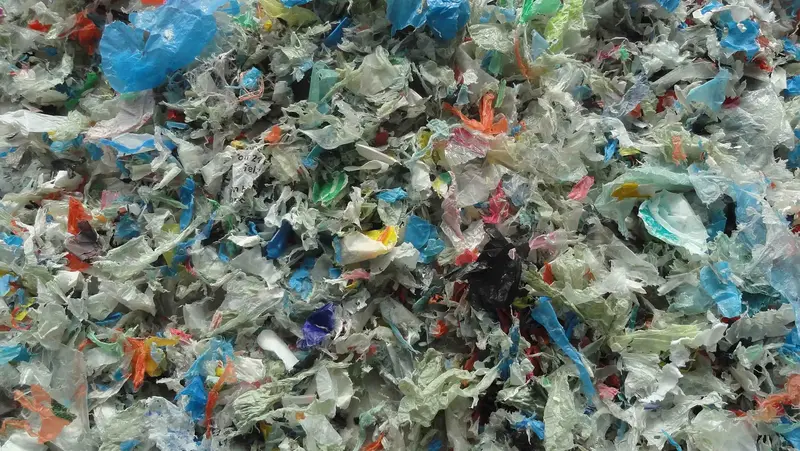
Lindner Advantages
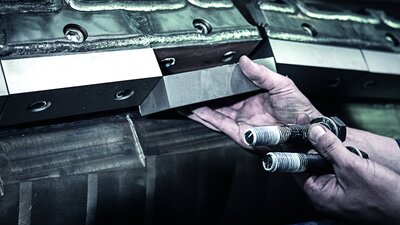
Single-Shaft Cutting System With Four-Fold Usable Solidly Built Square Knives
- Parts storage made easy thanks to identical knives for the rotor, counter knives and scraper
- Maximum uptimes ensured by four-fold usable, quick-change knive
- Low wear part costs thanks to four-fold usable square knive
- Easily adjustable cutting gap – even during operation – for consistently, high-quality output
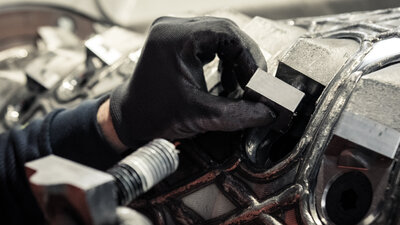
Countershaft Drive With Flywheel Energy Storage
Less energy consumption and more power thanks to the countershaft drive that stores and releases rotational energy depending on the load.
- Maximum energy efficiency
- Up to 2 x more throughput compared to drives without higher flywheel mass*
- Spare parts available worldwide
*University of Leoben, (2017). Independent report on the performance of different drive systems for shredding machines.